نقشهبرداری جریان ارزشیک تکنیک برای شناسایی و حذف ضایعات فرآیند است. این یک نوع خاص از نمودار جریان است که از نمادهایی به نام «زبان ناب» برای توصیف و بهبود جریان موجودی و اطلاعات استفاده میکند. این به ما کمک میکند تا بهترین ارزش را از طریق یک فرآیند کامل ایجاد ارزش به مشتریان ارائه دهیم و ضایعات را در جنبههای زیر به حداقل برسانیم:
- طراحی(از مفهوم تا مشتری)
- ساخت(از سفارش تا تحویل)
- پایداری (در حال استفاده در طول چرخه عمر تا خدمات)
ارزش برای مشتریان چیست؟
ارزش چیزی است که مشتری خریداری میکند که یک قابلیت ارائه شده به مشتری است. یک محصول یا خدمات ارائه شده به مشتری باید:
- از بالاترین کیفیت
- در زمان مناسب
- با قیمتی مناسب که توسط مشتری تعریف شده است
در واقع، فعالیتهایی که واقعاً برای مشتریان ارزش ایجاد میکنند تنها بخش کوچکی از کل فرآیند کاری هستند. به همین دلیل است که کسبوکارها باید بر کاهش فعالیتهای بیهوده تا حد ممکن تمرکز کنند. با انجام این کار، شرکتها میتوانند فرصتهای قابل توجهی برای بهبود عملکرد کلی خود شناسایی کنند.
ضایعات چیست؟
دانیل تی. جونز (1995) هفت نوع رایج از ضایعات را شناسایی میکند. این اصطلاحات از نامگذاری اصلی سیستم تولید تویوتا بهروز شدهاند:
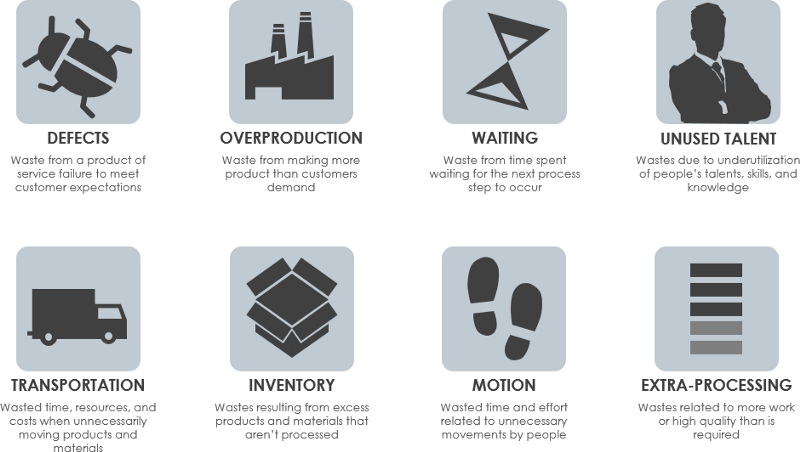
- موجودی:خرید و ذخیرهسازی مواد خام و انبار کردن کار در حال پیشرفت برای انتظار فرآیندهای آینده یک ضایعه است.
- انتظار:در یک سری مراحل برای پردازش یک ماده، اگر یکی از مراحل کند باشد، کار در حال پیشرفت انباشته میشود که یک ضایعه است.
- نقصها:در نهایت، مهمترین و رایجترین نوع نقصها هستند. نقصها برای مشتریان قابل قبول نیستند. برای جلوگیری از این، باید یک فرآیند کنترل کیفیت و فرآیند اصلاح ایجاد شود که به هزینه اضافه میکند. بنابراین نقصها یک شکل عمده از ضایعات هستند.
- بیشتولید:تولید اقلامی که بیش از تقاضای مشتری هستند.
- حرکت:حرکتهای غیرضروری ماشینآلات و حرکات اپراتورها میتواند باعث فرسودگی و خستگی شود.
- حمل و نقل:هر حرکت غیرضروری از کار در حال پیشرفت یا مواد خام یک نوع ضایعه است. این ممکن است به مواد آسیب برساند و همچنین ممکن است زمان چرخه تولید را افزایش دهد و بنابراین یک ضایعه است.
- بیشپردازش:ارائه ویژگیهایی که توسط مشتریان درخواست نشدهاند و تنظیم دقیق به سطوحی بیشتر از آنچه که توسط مشتریان تعیین شده است، به هزینه تولید اضافه میکند که یک ضایعه است.
تحلیل جریان ارزش چیست؟
نقشهبرداری جریان ارزش (VSM) یک تکنیک بنیادی برای شناسایی ضایعات و کاهش ضایعات فرآیند است. این یک ابزار ناب ضروری برای سازمانی است که میخواهد در حین سفر ناب خود برنامهریزی، اجرا و بهبود یابد. این به کاربران کمک میکند تا یک برنامه اجرایی محکم ایجاد کنند که منابع موجود آنها را به حداکثر برساند و اطمینان حاصل کند که مواد و زمان به طور کارآمد استفاده میشوند. تحلیل جریان ارزش یک ابزار برنامهریزی قدرتمند برای بهینهسازی نتیجه حذف ضایعات است.
VSM زمان و تلاشی که بر روی فعالیتهای غیرارزشافزا صرف میشود، هزینه انجام کسبوکار و زمینه را برای کاهش ضایعات و سادهسازی فرآیند فراهم میکند. هدف از نقشهبرداری جریان ارزش، حداکثر کردن ارزش و به حداقل رساندن ضایعات به چندین روش مختلف است، از جمله:
- تسهیل ارتباط و همکاری واضح
- تشویق به بهبود مستمر یک فرآیند
- امکان تغییر فرهنگ درون یک سازمان
- ایجاد تجسمهایی از تأخیرها، موجودی اضافی و محدودیتهای تولید
عملیات ارزش افزوده در مقابل عملیات غیر ارزش افزوده
حذف فعالیتهای بیهوده برای موفقیت شرکت شما حیاتی است. این فعالیتها میتوانند سودآوری را کاهش دهند، هزینههای مشتری را افزایش دهند، کیفیت را کاهش دهند و حتی رضایت کارکنان را تحت تأثیر قرار دهند. به همین دلیل، شما باید فعالیتهای غیرارزشافزا را شناسایی کرده و سعی کنید فرآیند را در جایی که ظاهر میشوند بهبود دهید یا در نهایت آنها را حذف کنید.
اشتباه نکنید. همه فعالیتهای بیهوده نمیتوانند از فرآیند کاری شما حذف شوند. برخی از آنها ضروری هستند.
موندن (1994) سه نوع عملیات را شناسایی میکند:
- عملیات غیرارزشافزا (NVA): اقداماتی که باید حذف شوند، مانند انتظار.
- ضروری اما غیرارزشافزا (NNVA): اقداماتی که بیهوده هستند اما تحت رویههای عملیاتی فعلی ضروری هستند.
- ارزشافزا (VA): تبدیل یا پردازش مواد خام از طریق کار دستی.
در نتیجه، فعالیتهای ارزشافزا باید بیشتر بهینهسازی شوند تا به دنبال بهبود مستمر و رشد یک سازمان باشند، در حالی که فعالیتهای غیرارزشافزا باید حذف شوند یا حداقل به حداقل ممکن برسند.
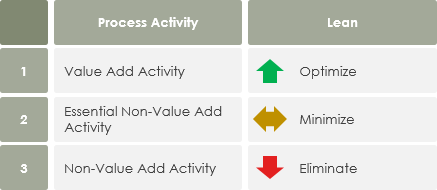
مثال ارزش و غیر ارزش افزوده — واریز پول در دستگاه خودپرداز
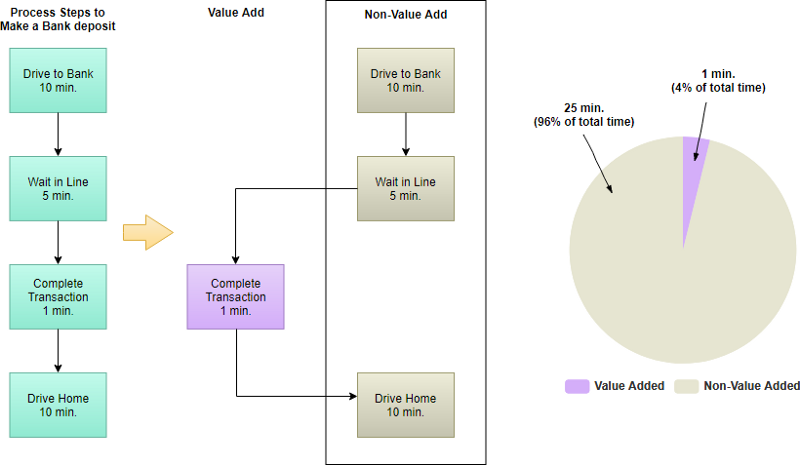
از نقشه جریان ارزش وضعیت فعلی به نقشه جریان ارزش وضعیت آینده
همانطور که قبلاً ذکر شد، تحلیل جریان ارزش یک ابزار برنامهریزی برای بهینهسازی نتایج حذف ضایعات است. اگر فقط یک نقشه وضعیت فعلی ایجاد کنید، هدف VSM را از دست دادهاید. نقشه وضعیت آینده تصویری از فرآیند تحول ناب برای یک جریان ارزش خاص است. قبل از اینکه نقشه وضعیت آینده را ایجاد کنید، باید قبلاً یک نقشه جریان ارزش وضعیت فعلی ایجاد کرده باشید.
بنابراین، تحلیل جریان ارزش بهصورت بصری جریان مراحل، تأخیرها و اطلاعات مورد نیاز برای ارائه یک محصول یا خدمات را ترسیم میکند؛ به این نقشه، نقشه «وضعیت فعلی» گفته میشود. نقشه وضعیت آینده به شناسایی بهبودهایی که باید در جریان ارزش انجام شود که زمان کلی تحویل را کوتاهتر کند، میپردازد.
برای ایجاد یک نقشه وضعیت آینده مؤثر، موارد زیر باید در نظر گرفته شود:
- یک محصول برای نقشهبرداری جریان ارزش انتخاب کنید
- یک نقشه جریان ارزش فعلی ایجاد کنید
- ضایعات را حذف کنید و یک نقشه وضعیت آینده کارآمدتر ایجاد کنید
- یک برنامه اجرایی ایجاد کنید
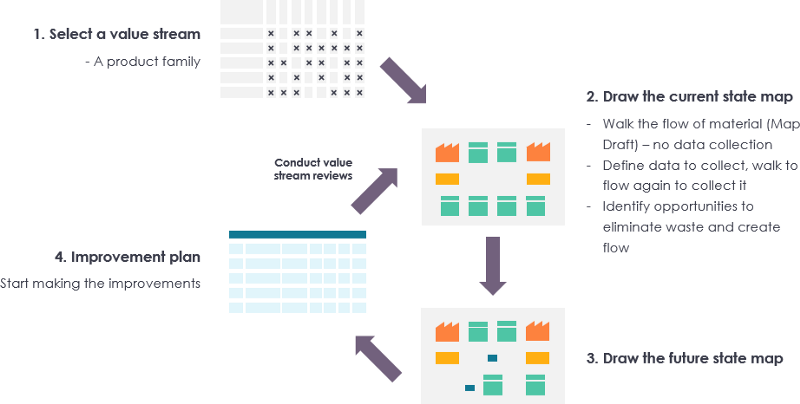
در نهایت، شما باید یک برنامه اجرایی برای جریان ارزش ایجاد کنید تا به وضعیت آینده دست یابید. اکنون شما با یک برنامه برای یک جریان ارزش لاغر مسلح هستید که میتوانید از آن برای پیگیری/اندازهگیری بهبودهای خود در طول سال استفاده کنید. اطمینان حاصل کنید که یک «مدیر جریان ارزش» یا مدیر پروژه دارید که برنامه را به اتمام برساند.
مثال تحلیل جریان ارزش — کنترل تولید
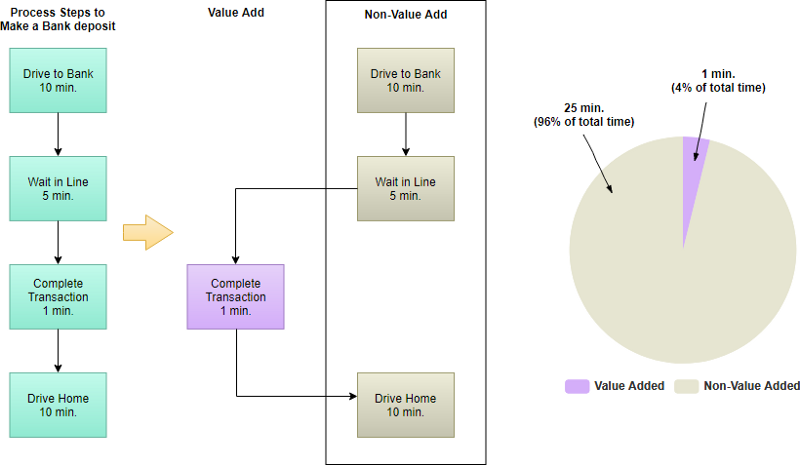
نقشهبرداری جریان ارزش — مثال دیگر
نقشههای جریان ارزش میتوانند با دنبال کردن مراحل زیر ایجاد شوند:
- اولین مرحله در نقشهبرداری جریان ارزش، ترسیم جعبههای فرآیند برای مراحل مختلف فرآیند است، که از سمت تأمینکننده شروع شده و به سمت مشتری در ناحیه جریانهای اطلاعات میرود.
- مرحله دوم، ترسیم انواع مختلف جعبههای فرآیند برای انواع مختلف مراحل تولید در بخش جریان اطلاعات به نام جریانهای مواد است.
- سومین مرحله در نقشهبرداری جریان ارزش، جعبههای داده است که درست زیر هر یک از مراحل فرآیند (یا مراحل تولید) قرار دارد، که در آن دادههای هر یک از مراحل فرآیند ترسیم شده در نقشه ثبت میشود. اطلاعاتی که ممکن است برای طراحی VSM جالب باشد، میتواند در اینجا قرار گیرد.
- مرحله چهارم، ترسیم روشهای اتصال بین جعبههای فرآیند است.
- مرحله پنجم به توصیف پیوند مشتریان و تأمینکنندگان به فرآیند میپردازد.
- مرحله پنج، نردبان زمان تحویل در پایین VSM است که جنبههای مختلف زمان در جریان ارزش را نشان میدهد.
مثال زیر نشان میدهد که یک نقشه جریان ارزش معمولی چگونه ممکن است به نظر برسد:
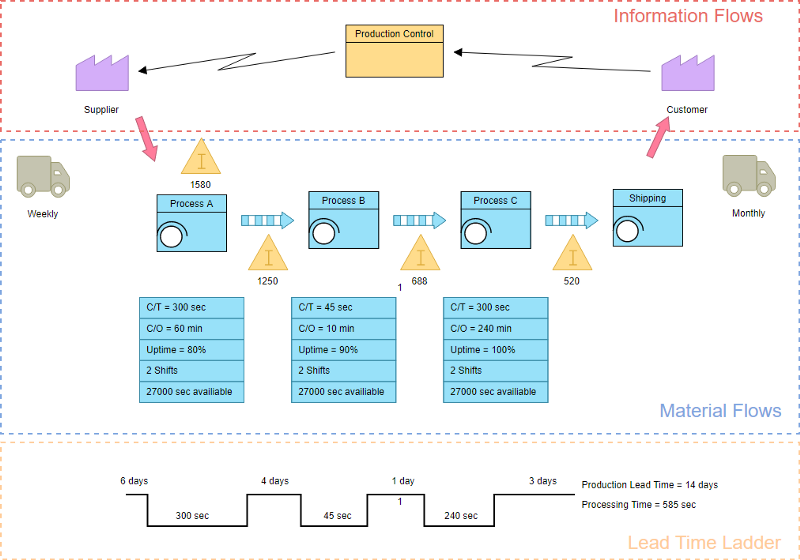
توسعه یک برنامه اجرایی مستمر
VSM به کاربران کمک میکند تا یک برنامه اجرایی محکم ایجاد کنند که منابع موجود آنها را به حداکثر برساند و به اطمینان از استفاده مؤثر از مواد و زمان کمک کند. بر اساس اطلاعاتی که نقشه آینده ارائه کرده است، اکنون میتوانیم یک برنامه اجرایی برای اقداماتی که برای انتقال از وضعیت فعلی به وضعیت آینده نیاز است، توسعه دهیم. در اینجا یک الگوی عمومی ارائه شده است:
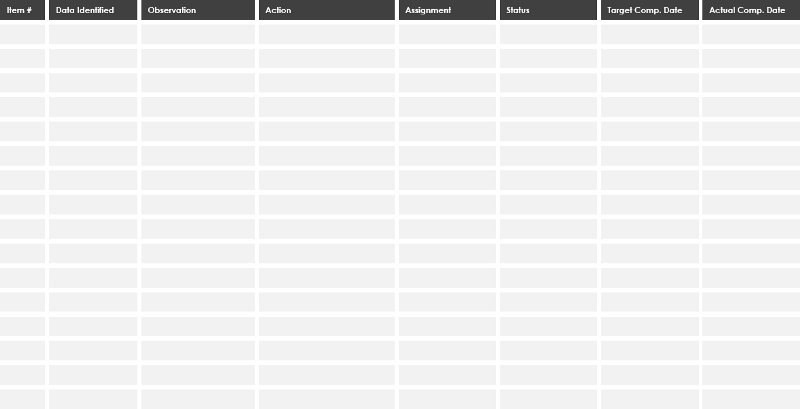
اجزای نقشهبرداری جریان ارزش
نمادها / توضیحات

مشتری/تأمینکننده: تأمینکننده را زمانی که در بالا سمت چپ است، و مشتری را زمانی که در بالا سمت راست است، نشان میدهد، نقطه پایانی معمول برای مواد

جریان فرآیند اختصاصی: یک فرآیند، عملیات، ماشین یا دپارتمان که از طریق آن مواد جریان مییابد. این نمایانگر یک دپارتمان با جریان داخلی ثابت و پیوسته است.

فرآیند مشترک: یک فرآیند، عملیات، دپارتمان، یا فرآیند مشترک: یک فرآیند، عملیات، یا دپارتمانی که سایر خانوادههای جریان ارزش با آن مشترک هستند.

جعبه داده: حاوی اطلاعات/دادههای مهم مورد نیاز برای تحلیل و مشاهده سیستم است.

سلول کاری: نشان میدهد که چندین فرآیند در یک سلول کاری تولیدی ادغام شدهاند.

موجودی: موجودی بین دو فرآیند را نشان میدهد

محصولات ارسال شده: نمایانگر حرکت مواد خام از تأمینکنندگان به داکهای دریافت کارخانه است. یا، حرکت کالاهای آماده از داکهای ارسال کارخانه به مشتریان

پیکان فشار: نمایانگر «فشار دادن» مواد از یک فرآیند به فرآیند بعدی است.

سوپرمارکت: یک «سوپرمارکت» موجودی.

کشیدن مواد: سوپرمارکتها با این «کشیدن» که نشاندهنده حذف فیزیکی است، به فرآیندهای پاییندست متصل میشوند.

مسیر FIFO: موجودی اول وارد، اول خارج. از آن استفاده کنید زمانی که فرآیندها با یک سیستم FIFO که ورودی را محدود میکند، متصل هستند.

موجودی ایمنی: نمایانگر یک «پوشش» موجودی (یا موجودی ایمنی) در برابر مشکلاتی مانند زمانهای غیرکاری، برای محافظت از سیستم در برابر نوسانات ناگهانی در سفارشات مشتری یا خرابیهای سیستم است.

محصولات ارسال شده خارجی: ارسالها از تأمینکنندگان یا به مشتریان با استفاده از حمل و نقل خارجی

کنترل تولید: این جعبه نمایانگر یک بخش مرکزی برنامهریزی یا کنترل تولید، شخص یا عملیات است.

اطلاعات دستی: یک پیکان باریک و مستقیم جریان کلی اطلاعات را از یادداشتها، گزارشها یا مکالمات نشان میدهد. فرکانس و یادداشتهای دیگر ممکن است مرتبط باشند.

اطلاعات الکترونیکی: این پیکان موجدار نمایانگر جریان الکترونیکی مانند تبادل دادههای الکترونیکی (EDI)، اینترنت، اینترانتها، شبکههای محلی (LAN) و شبکههای گسترده (WAN) است. شما میتوانید فرکانس تبادل اطلاعات/دادهها، نوع رسانههای استفاده شده مانند فکس، تلفن و غیره و نوع دادههای مبادله شده را مشخص کنید.

کانبان تولید: این کانبان تولید یک تعداد مشخص از قطعات را تحریک میکند. این سیگنال یک فرآیند تأمین را برای ارائه قطعات به یک فرآیند پاییندست نشان میدهد.

کانبان برداشت شده: این کانبان نمایانگر یک کارت یا دستگاه است که به یک کارگر مواد دستور میدهد تا قطعات را از سوپرمارکت به فرآیند دریافت منتقل کند. کارگر مواد (یا اپراتور) به سوپرمارکت میرود و اقلام مورد نیاز را برداشت میکند.

کانبان سیگنال: هرگاه سطح موجودی در سوپرمارکت بین دو فرآیند به یک نقطه تحریک یا حداقل کاهش یابد، از این کانبان استفاده میشود. این کانبان همچنین به عنوان کانبان «یک در هر دسته» شناخته میشود.

پست کانبان: یک مکان که سیگنالهای کانبان برای برداشت در آن قرار دارند. اغلب با سیستمهای دوکارتی برای تبادل کانبان برداشت و تولید استفاده میشود.

کشیدن توالی: نمایانگر یک سیستم کششی است که به فرآیندهای زیرمجموعه دستور میدهد تا نوع و مقدار مشخصی از محصول، معمولاً یک واحد، را بدون استفاده از سوپرمارکت تولید کنند.

تراز کردن بار: ابزاری برای دستهبندی کانبان به منظور تراز کردن حجم تولید و ترکیب در طول زمان.

بروید و تولید را ببینید: جمعآوری اطلاعات از طریق وسایل بصری

اطلاعات کلامی: نمایانگر جریان اطلاعات کلامی یا شخصی است.

کایزن: برای برجسته کردن نیازهای بهبود و برنامهریزی کارگاههای کایزن در فرآیندهای خاص که برای دستیابی به نقشه وضعیت آینده جریان ارزش حیاتی هستند، استفاده میشود.

اپراتور: نمایانگر یک اپراتور است. این نشان میدهد که چند اپراتور برای پردازش خانواده VSM در یک ایستگاه کاری خاص نیاز است.

اطلاعات دیگر: اطلاعات دیگر مفید یا بالقوه مفید.

زمانبندی: زمانهای ارزش افزوده (زمانهای چرخه) و زمانهای غیر ارزش افزوده (انتظار) را نشان میدهد. از این برای محاسبه زمان سرب و زمان کل چرخه استفاده کنید.
اصطلاحات نقشه جریان ارزش
- C/T (زمان چرخه): زمان چرخه پردازنده = زمان لازم برای تکمیل یک وظیفه.
- P/T یا C/O (زمان تغییر): زمان غیر ارزش افزوده لازم برای تبدیل یک خط از یک محصول به محصول دیگر، زمان تغییر یا زمان راهاندازی برای شروع یک وظیفه جدید.
- VA (وظیفه ارزش افزوده): زمان ارزش افزوده یا زمان لازم برای تکمیل یک وظیفه ضروری.
- NVA (وظیفه غیر ارزش افزوده): زمان غیر ارزش افزوده = PT — VAT.
- L/T (زمان سرب): زمان سرب، یا زمان کل از زمانی که یک وظیفه در یک مرکز کاری شروع میشود تا زمانی که از مرکز کاری خارج میشود.
- FTT (کیفیت اولین بار): کیفیت اولین بار یا بازده کیفیت اولین بار.
- T/T (زمان تاکت): زمان تولید متوسط واحد لازم برای برآورده کردن تقاضای مشتری.
- ظرفیت: یک معیار که نشان میدهد فرآیند کندترین شما چند قطعه در روز میتواند مدیریت کند.
ابزار نقشهبرداری جریان ارزش
به دنبال نرمافزار VSM هستید؟نرمافزار نقشهبرداری جریان ارزش Visual Paradigmشما میتوانید به راحتی و به سرعت نقشهبرداری ارزش حرفهای ایجاد کنید. ابزار نقشهبرداری ارزش با مجموعهای غنی از نمادهای نقشهبرداری ارزش همراه است. با ویرایشگر VSM کشیدن و رها کردن و مجموعهای قدرتمند از ویژگیها، میتوانید به راحتی نقشههای ارزش حرفهای ایجاد کنید.
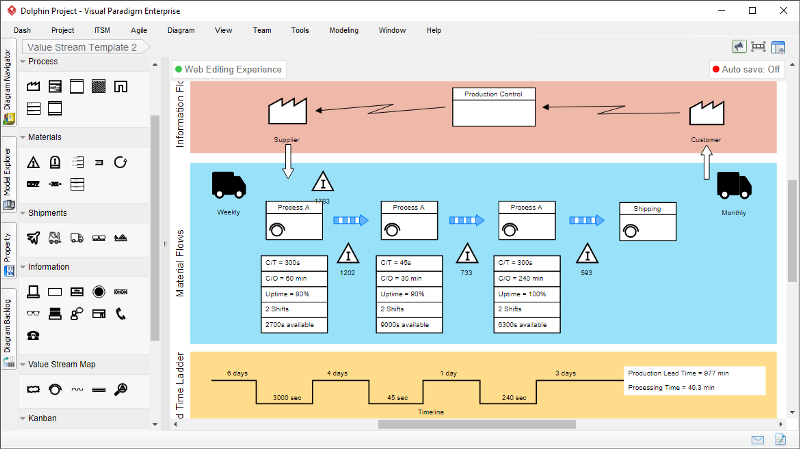
یادگیری از طریق مثالها — الگوهای نقشهبرداری ارزش
شما میتوانید با کلیک بر روی لینک مثال زیر، آنها را به صورت آنلاین امتحان و ویرایش کنید:
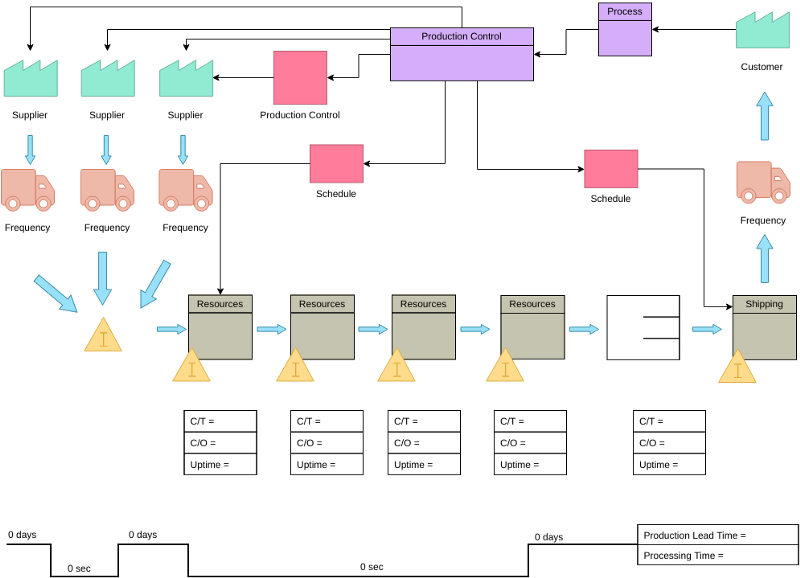
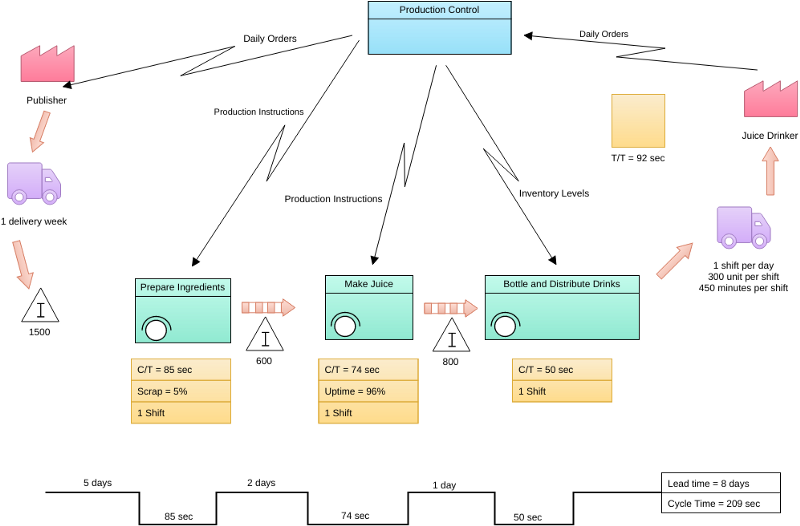
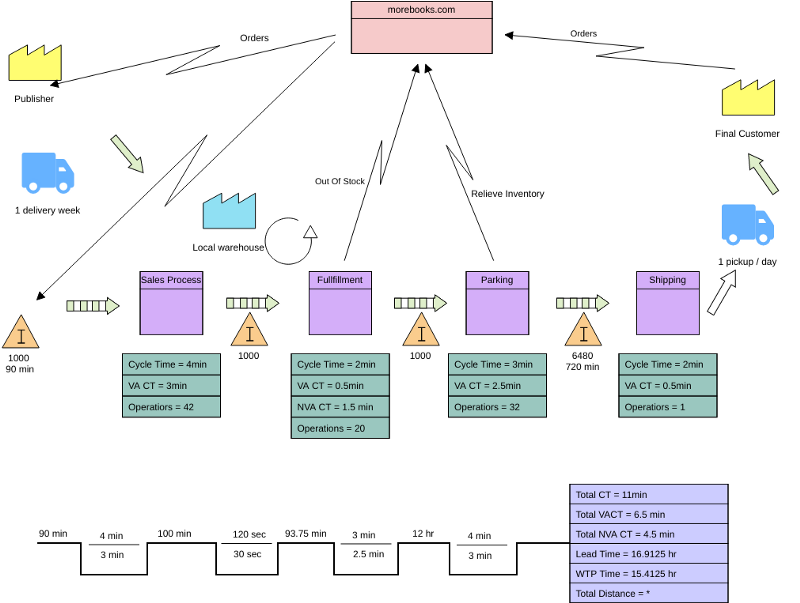
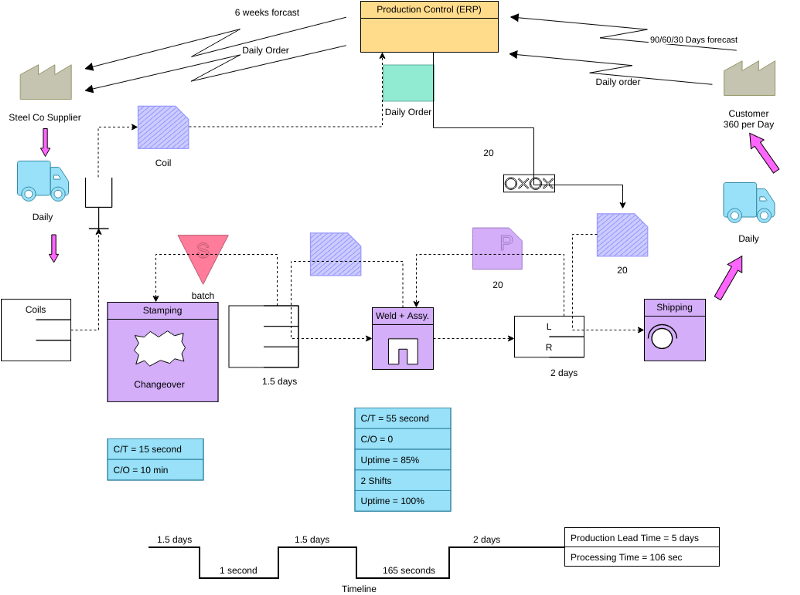
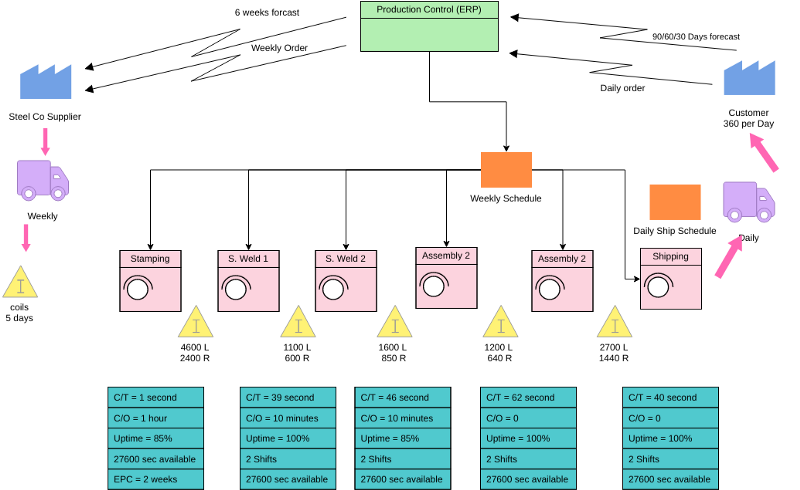

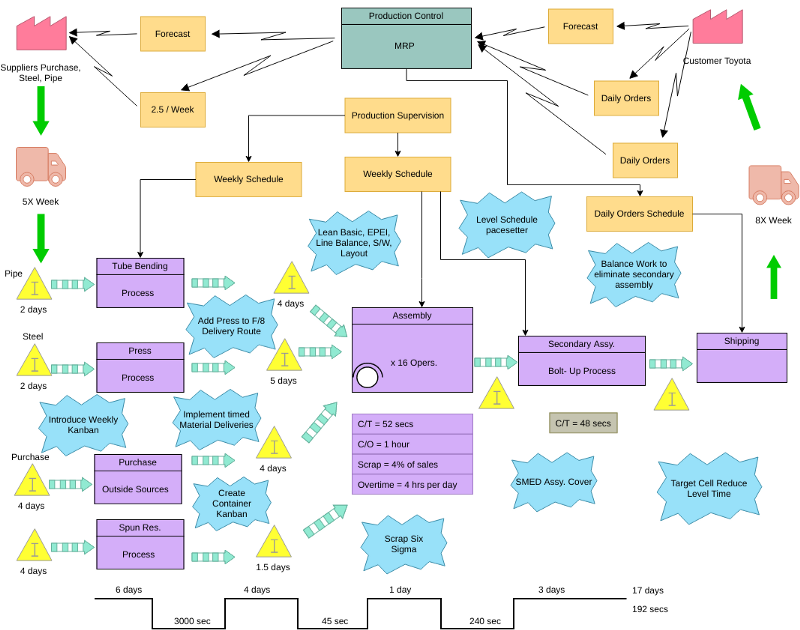
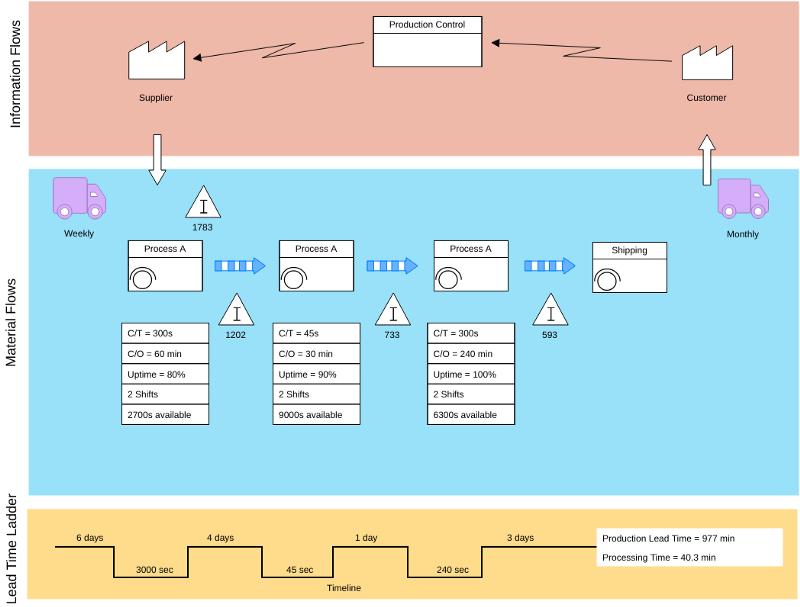
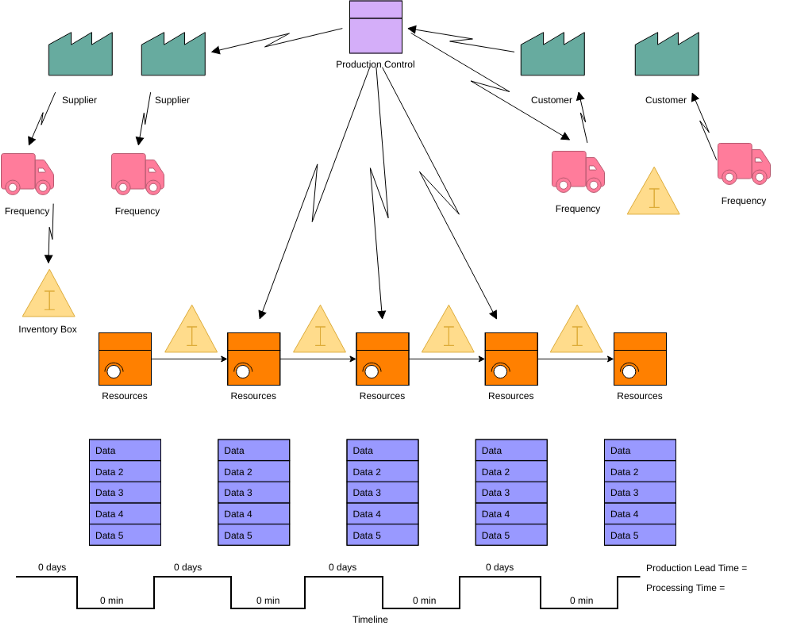
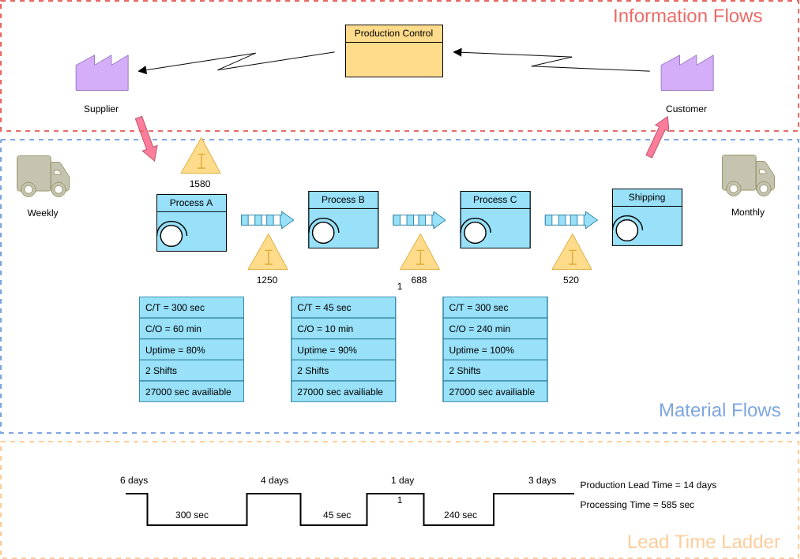
This post is also available in Deutsch, English, Español, Français, Bahasa Indonesia, 日本語, Polski, Portuguese, Ру́сский, Việt Nam, 简体中文 and 繁體中文.