- Desain (Dari Konsep ke Pelanggan)
- Bangun (Dari Pesanan ke Pengiriman)
- Pelihara (Dalam Penggunaan Sepanjang Siklus Hidup hingga Layanan)
Apa itu Nilai bagi Pelanggan?
Nilai adalah apa yang dibeli pelanggan, yang merupakan kemampuan yang diberikan kepada mereka. Produk atau layanan yang diberikan kepada pelanggan seharusnya:
- Dengan Kualitas Tertinggi
- Pada Waktu yang Tepat
- Dengan Harga yang Sesuai Seperti Didefinisikan oleh Pelanggan
Nyatanya, aktivitas-aktivitas yang benar-benar menghasilkan nilai bagi pelanggan hanyalah sebagian kecil dari seluruh proses kerja. Inilah sebabnya mengapa bisnis harus fokus pada pengurangan aktivitas yang boros sebanyak mungkin. Dengan melakukan hal tersebut, perusahaan dapat mengidentifikasi peluang signifikan untuk meningkatkan kinerja secara keseluruhan.
Apa itu Pemborosan?
Daniel T. Jones (1995) mengidentifikasi tujuh jenis pemborosan yang umum diterima. Istilah-istilah ini diperbarui dari nomenklatur asli sistem produksi Toyota:
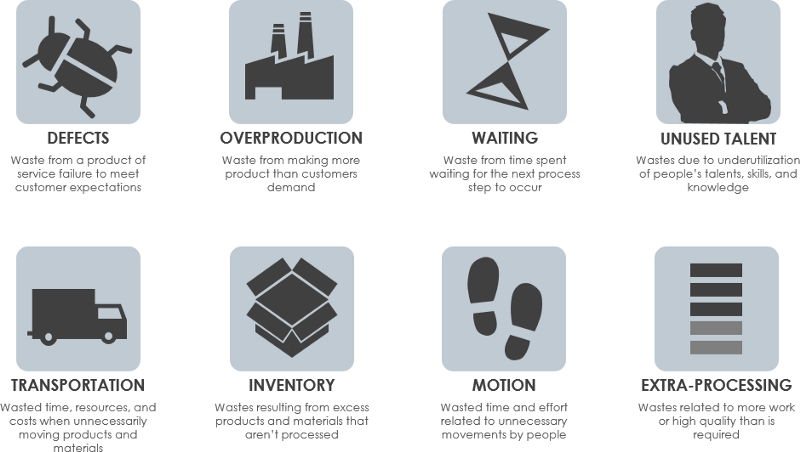
- Persediaan: Membeli dan menyimpan bahan mentah, serta menyimpan pekerjaan yang sedang diproses untuk menunggu proses berikutnya adalah pemborosan.
- Menunggu: Dalam serangkaian langkah untuk memproses bahan, jika salah satu langkah berjalan lambat, maka akan terjadi penumpukan pekerjaan dalam proses yang merupakan pemborosan.
- Cacat: Akhirnya, jenis yang paling penting dan umum adalah cacat. Cacat tidak dapat diterima oleh pelanggan. Untuk menghindari ini, proses pengecekan kualitas dan proses perbaikan harus diberlakukan, yang menambah biaya. Oleh karena itu, cacat merupakan bentuk pemborosan yang utama.
- Produksi Berlebih: Memproduksi barang yang melebihi permintaan pelanggan.
- Gerakan: Pergerakan yang tidak perlu dari mesin dan pergerakan operator dapat menyebabkan keausan dan kelelahan.
- Transportasi: Setiap perpindahan yang tidak perlu dari pekerjaan dalam proses atau bahan mentah merupakan bentuk pemborosan. Hal ini dapat menyebabkan kerusakan pada bahan dan juga meningkatkan waktu siklus produksi, sehingga merupakan pemborosan.
- Proses Berlebih: Menyediakan fitur yang tidak diminta oleh pelanggan, dan penyempurnaan hingga level yang lebih tinggi daripada yang ditetapkan oleh pelanggan, menambah biaya manufaktur yang merupakan pemborosan.
Apa Itu Analisis Aliran Nilai?
Pemetaan Aliran Nilai (VSM) adalah teknik dasar untuk mengidentifikasi pemborosan dan mengurangi pemborosan proses. Ini adalah alat lean yang penting bagi organisasi yang ingin merencanakan, menerapkan, dan meningkatkan kinerjanya dalam perjalanan lean-nya. Alat ini membantu pengguna membuat rencana implementasi yang solid untuk memaksimalkan sumber daya yang tersedia dan memastikan bahwa bahan serta waktu digunakan secara efisien. Analisis Aliran Nilai adalah alat perencanaan yang kuat untuk mengoptimalkan hasil dari penghilangan pemborosan.
VSM menjelaskan dengan jelas waktu dan usaha yang dihabiskan untuk aktivitas yang tidak menambah nilai, biaya operasional, serta menetapkan langkah untuk mengurangi pemborosan dan menyederhanakan proses. Tujuan pemetaan aliran nilai adalah untuk memaksimalkan nilai dan meminimalkan pemborosan dengan beberapa cara, antara lain:
- Memfasilitasi komunikasi dan kolaborasi yang jelas
- Mendorong perbaikan berkelanjutan pada suatu proses
- Memungkinkan perubahan budaya dalam organisasi
- Membuat visualisasi dari keterlambatan, kelebihan persediaan, dan kendala produksi
Operasi Bernilai Tambah vs. Operasi Tidak Bernilai Tambah
Menghilangkan aktivitas yang boros sangat penting untuk keberhasilan perusahaan Anda. Aktivitas tersebut dapat menurunkan profitabilitas, meningkatkan biaya bagi pelanggan, mengurangi kualitas, bahkan kepuasan karyawan. Untuk alasan ini, Anda perlu mengidentifikasi aktivitas yang tidak menambah nilai dan berusaha memperbaiki proses di mana aktivitas tersebut muncul atau menghilangkannya sepenuhnya.
Jangan salah. Tidak semua aktivitas yang boros dapat dihilangkan dari proses kerja Anda. Beberapa di antaranya memang diperlukan.
Monden (1994) mengidentifikasi tiga jenis operasi:
- Operasi Tidak Menambah Nilai (NVA): Tindakan yang seharusnya dihilangkan, seperti menunggu.
- Yang Diperlukan Tetapi Tidak Menambah Nilai (NNVA): Tindakan yang boros namun diperlukan dalam prosedur operasional saat ini.
- Menambah Nilai (VA): Konversi atau pemrosesan bahan mentah melalui tenaga kerja manual.
Kesimpulannya, aktivitas yang menambah nilai harus dioptimalkan lebih lanjut untuk perbaikan berkelanjutan dan pertumbuhan organisasi, sementara aktivitas yang tidak menambah nilai harus dihilangkan atau setidaknya diminimalkan sebanyak mungkin.
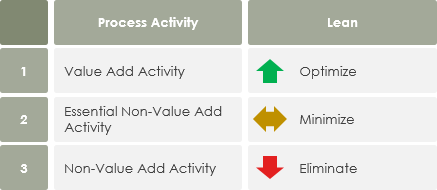
Contoh Aktivitas Bernilai Tambah dan Tidak Bernilai Tambah — Menyetor Uang di ATM
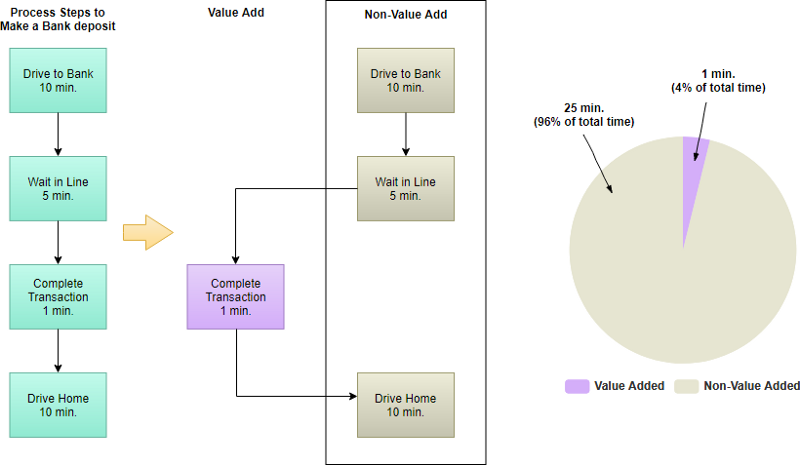
Dari Peta Aliran Nilai Kondisi Saat Ini ke Peta Aliran Nilai Kondisi Masa Depan
Seperti yang telah disebutkan sebelumnya, Analisis Aliran Nilai adalah alat perencanaan untuk mengoptimalkan hasil penghilangan pemborosan. Jika Anda hanya membuat peta kondisi saat ini, maka tujuan VSM belum tercapai. Peta kondisi masa depan adalah gambaran proses transformasi lean untuk suatu aliran nilai tertentu. Sebelum membuat peta kondisi masa depan, Anda harus sudah membuat peta aliran nilai kondisi saat ini.
Dengan demikian, Analisis Aliran Nilai secara visual memetakan aliran langkah, keterlambatan, dan informasi yang diperlukan untuk mengantarkan produk atau layanan; ini disebut peta “Kondisi Saat Ini”. Peta kondisi masa depan mengidentifikasi perbaikan yang perlu dilakukan pada aliran nilai guna mempersingkat waktu penyelesaian secara keseluruhan.
Untuk membuat peta kondisi masa depan yang efektif, hal-hal berikut harus dipertimbangkan:
- Pilih Produk untuk Pemetaan Aliran Nilai
- Buat Peta Aliran Nilai Kondisi Saat Ini
- Hilangkan Pemborosan dan Buat Peta Kondisi Masa Depan yang Lebih Efisien
- Buat Rencana Implementasi
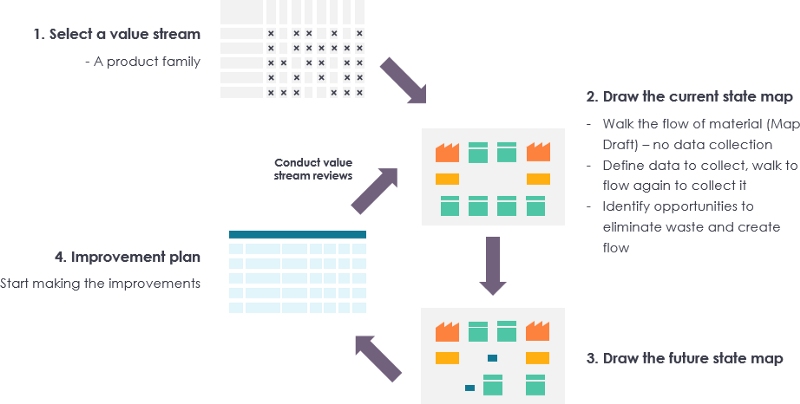
Akhirnya, Anda harus membuat rencana implementasi aliran nilai untuk mencapai kondisi masa depan. Anda sekarang dilengkapi dengan rencana untuk aliran nilai lean yang dapat Anda gunakan untuk melacak dan mengukur perbaikan Anda sepanjang tahun. Pastikan Anda memiliki “manajer aliran nilai” atau manajer proyek yang mengarahkan rencana tersebut hingga selesai.
Contoh Analisis Aliran Nilai — Pengendalian Produksi
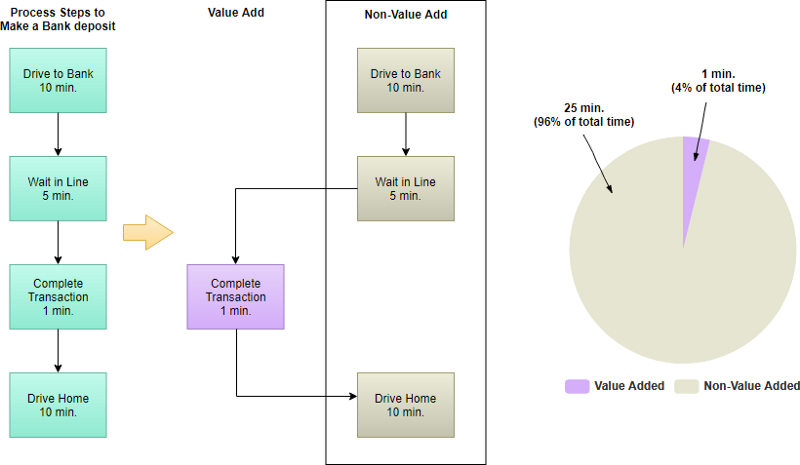
Pemetaan Aliran Nilai — Contoh Lain
Peta aliran nilai dapat dibuat dengan mengikuti langkah-langkah berikut:
- Langkah pertama dalam pemetaan aliran nilai adalah menggambar KOTAK PROSES untuk berbagai tahap proses, dimulai dari sisi pemasok hingga sisi pelanggan di area aliran informasi.
- Langkah kedua adalah menggambar berbagai jenis kotak proses untuk berbagai tahap produksi di bawah bagian aliran informasi yang disebut Aliran Material.
- Langkah ketiga dalam pemetaan aliran nilai adalah KOTAK DATA tepat di bawah masing-masing proses (atau tahap produksi), di mana data dari setiap tahap proses yang digambar dicatat. Informasi yang mungkin menarik untuk desain VSM dapat ditempatkan di sini.
- Langkah keempat adalah menggambar METODE KONNEKSI antara kotak-kotak proses.
- Langkah kelima menggambarkan penghubungan PELANGGAN DAN PEMASOK ke dalam proses.
- Langkah keenam adalah TANGGA WAKTU pada bagian bawah VSM, yang menunjukkan berbagai aspek waktu dalam aliran nilai.
Contoh di bawah ini menunjukkan seperti apa peta aliran nilai yang khas:
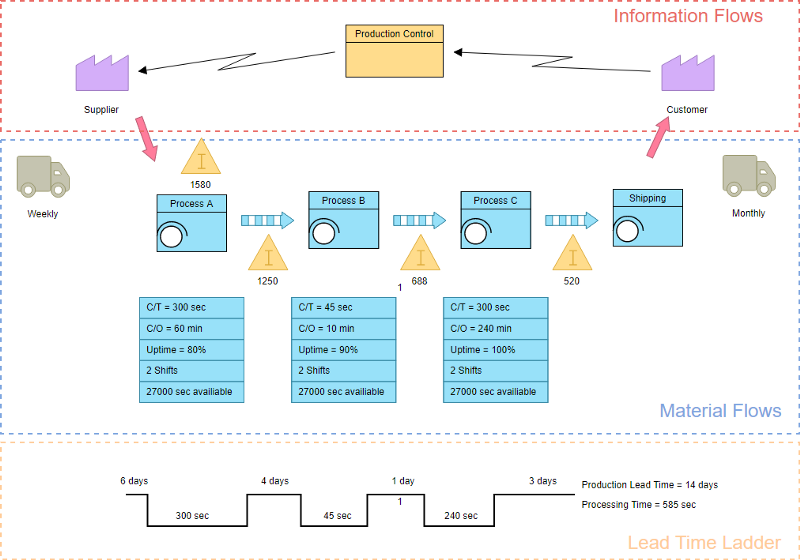
Edit Diagram Ini
Mengembangkan Rencana Implementasi Berkelanjutan
VSM membantu pengguna membuat rencana implementasi yang solid untuk memaksimalkan sumber daya yang tersedia dan memastikan bahwa bahan serta waktu digunakan secara efisien. Berdasarkan informasi yang diberikan oleh peta kondisi masa depan, kita sekarang dapat mengembangkan rencana implementasi untuk tindakan yang diperlukan guna berpindah dari kondisi saat ini ke kondisi masa depan. Berikut adalah template umum yang disediakan:
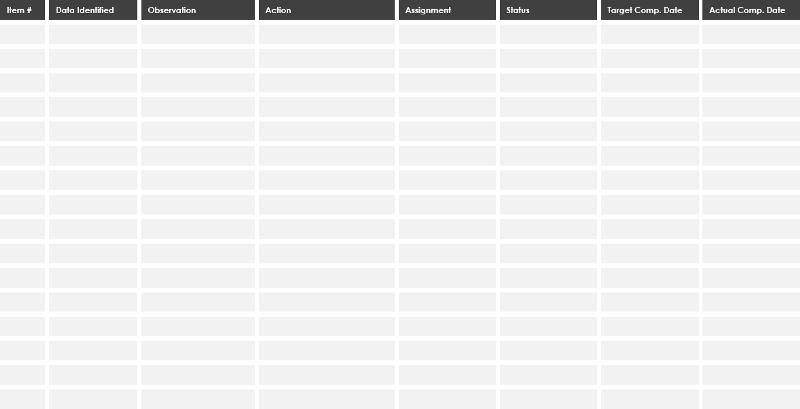
Komponen Pemetaan Aliran Nilai
Simbol / Deskripsi

Pelanggan/Pemasok: mewakili Pemasok ketika berada di kiri atas, dan pelanggan ketika berada di kanan atas, yang merupakan titik akhir standar bagi material.

Aliran Proses Khusus: proses, operasi, mesin, atau departemen yang dilalui material. Ini mewakili satu departemen dengan aliran internal yang berkelanjutan dan tetap.

Proses Bersama: proses, operasi, atau departemen yang dibagi oleh keluarga aliran nilai lainnya.

Kotak Data: berisi informasi/data penting yang diperlukan untuk menganalisis dan mengamati sistem.

Sel Kerja: menunjukkan bahwa beberapa proses telah diintegrasikan ke dalam sebuah sel kerja manufaktur.

Persediaan: menunjukkan persediaan antara dua proses.

Pengiriman: mewakili pergerakan bahan mentah dari pemasok ke dermaga penerimaan di pabrik, atau pergerakan barang jadi dari dermaga pengiriman pabrik ke pelanggan.

Panah Dorong: mewakili “pendorongan” material dari satu proses ke proses berikutnya.

Supermarket: sebuah “supermarket” persediaan.

Tarikan Material: supermarket terhubung ke proses hilir dengan “tarikan” yang menunjukkan pengambilan fisik.

Jalur FIFO: persediaan First-In-First-Out. Gunakan saat proses terhubung dengan sistem FIFO yang membatasi input.

Stok Pengaman: mewakili perlindungan persediaan (atau stok pengaman) terhadap masalah seperti waktu henti, untuk melindungi sistem dari fluktuasi mendadak dalam pesanan pelanggan atau kegagalan sistem.

Pengiriman Eksternal: pengiriman dari pemasok atau kepada pelanggan dengan menggunakan transportasi eksternal.

Pengendalian Produksi: kotak ini mewakili departemen penjadwalan atau pengendalian produksi pusat, orang, atau operasi.

Informasi Manual: panah lurus tipis menunjukkan aliran umum informasi dari memo, laporan, atau percakapan. Frekuensi dan keterangan lain mungkin relevan.

Informasi Elektronik: panah bergelombang ini mewakili aliran elektronik seperti pertukaran data elektronik (EDI), Internet, Intranet, LAN, atau WAN. Anda dapat menunjukkan frekuensi pertukaran informasi/data, jenis media yang digunakan (misalnya faks, telepon, dll), dan jenis data yang dipertukarkan.

Kanban Produksi: memicu produksi sejumlah bagian yang telah ditentukan. Ini memberi sinyal kepada proses pemasokan untuk menyediakan bagian ke proses hilir.

Kanban Ditarik: mewakili kartu atau perangkat yang menginstruksikan penangan material untuk memindahkan bagian dari supermarket ke proses penerimaan. Penangan material (atau operator) pergi ke supermarket dan mengambil barang yang diperlukan.

Kanban Sinyal: digunakan setiap kali tingkat persediaan di tangan pada supermarket antara dua proses turun ke titik pemicu atau minimum. Ini juga disebut sebagai Kanban “satu-per-batch”.

Pos Kanban: lokasi di mana sinyal Kanban ditempatkan untuk diambil. Sering digunakan dengan sistem dua kartu untuk menukarkan Kanban penarikan dan produksi.

Tarik Urutan: mewakili sistem tarik yang memberikan instruksi kepada proses perakitan untuk memproduksi jenis dan jumlah produk yang telah ditentukan, biasanya satu unit, tanpa menggunakan supermarket.

Penyeimbangan Beban: alat untuk mengelompokkan Kanban guna menyeimbangkan volume dan campuran produksi selama periode tertentu.

Perhatikan Produksi: pengumpulan informasi melalui cara visual.

Informasi Lisan: mewakili aliran informasi secara lisan atau pribadi.

Kaizen: digunakan untuk menyoroti kebutuhan perbaikan dan merencanakan lokakarya kaizen pada proses-proses tertentu yang penting untuk mencapai Peta Kondisi Masa Depan dari aliran nilai.

Operator: mewakili operator. Menunjukkan jumlah operator yang diperlukan untuk memproses keluarga VSM di suatu stasiun kerja tertentu.

Informasi Lainnya: informasi lain yang berguna atau berpotensi berguna.

Garis Waktu: menunjukkan waktu bernilai tambah (waktu siklus) dan waktu tidak bernilai tambah (waktu tunggu). Gunakan ini untuk menghitung Lead Time dan Total Cycle Time.
Terminologi Peta Aliran Nilai
- C/T (Waktu Siklus): Waktu siklus prosesor = waktu untuk menyelesaikan suatu tugas.
- P/T atau C/O (Waktu Ganti): Waktu tidak bernilai tambah yang diperlukan untuk mengubah lini dari satu produk ke produk lain, atau waktu setup untuk memulai tugas baru.
- VA (Tugas Bernilai Tambah): Waktu bernilai tambah atau waktu yang dibutuhkan untuk menyelesaikan tugas yang diperlukan.
- NVA (Tugas Tidak Bernilai Tambah): Waktu tidak bernilai tambah = PT – VAT.
- L/T (Lead Time): Total waktu dari saat tugas dimulai di dalam pusat kerja hingga tugas tersebut selesai.
- FTT (Pertama Kali Selesai): Kualitas pada pengulangan pertama atau hasil kualitas pertama kali.
- T/T (Waktu Takt): Rata-rata waktu produksi per unit yang dibutuhkan untuk memenuhi permintaan pelanggan.
- Kapasitas: Metode yang menunjukkan berapa banyak bagian per hari yang dapat ditangani oleh proses paling lambat.
Alat Pemetaan Aliran Nilai
Mencari perangkat lunak VSM? Perangkat lunak pemetaan aliran nilai Visual Paradigm dapat dengan mudah dan cepat membuat peta aliran nilai profesional. Alat pemetaan aliran nilai dilengkapi dengan kumpulan simbol khusus. Dengan editor VSM yang dapat di-drag dan drop serta set fitur yang kuat, Anda dapat dengan mudah membuat peta aliran nilai profesional.
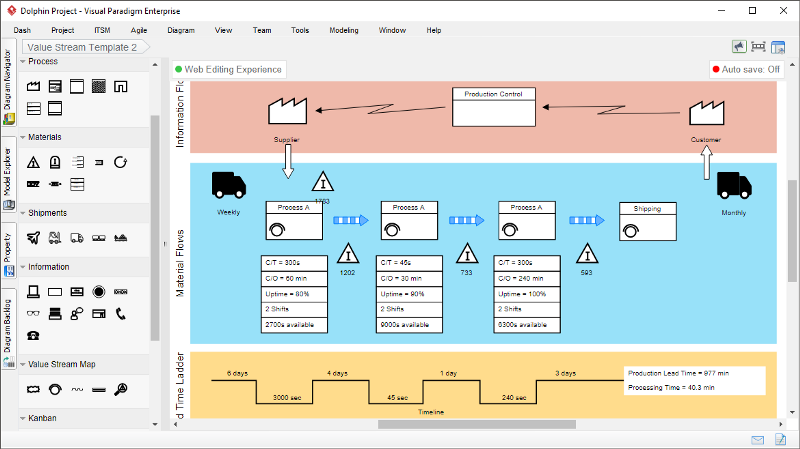
Belajar dari Contoh — Template Pemetaan Aliran Nilai
Anda dapat mencoba dan mengeditnya secara online dengan mengklik tautan contoh di bawah ini:
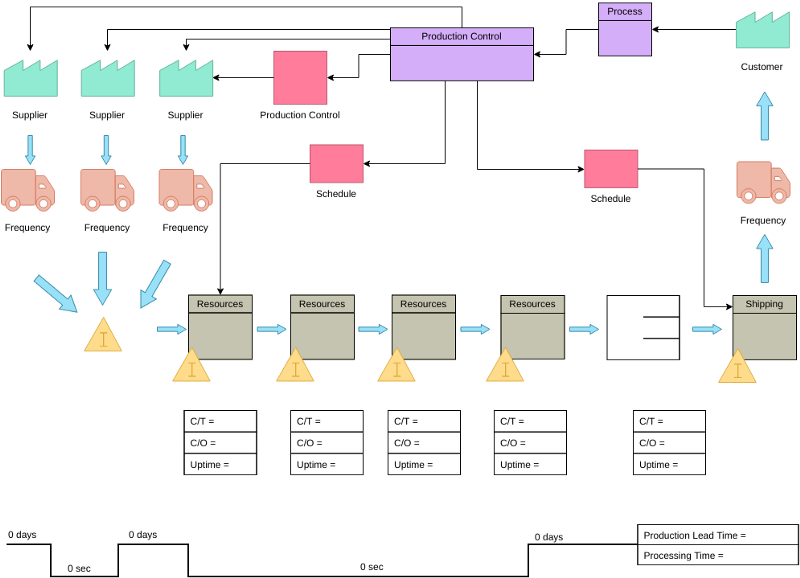
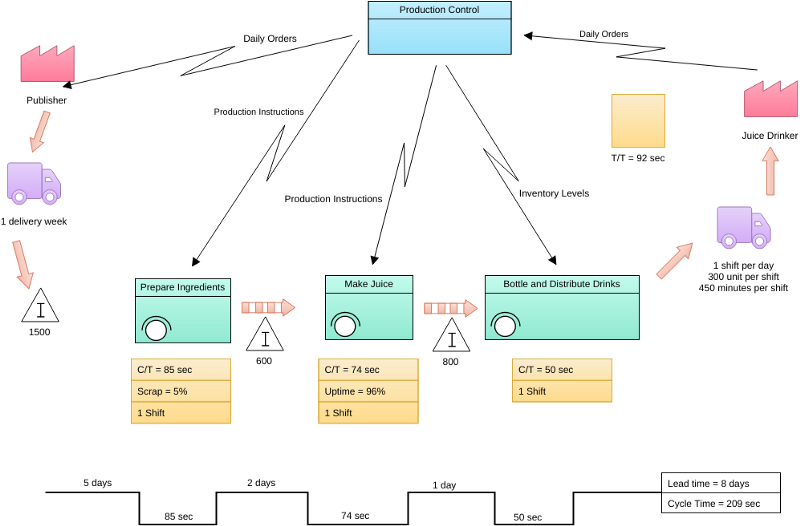
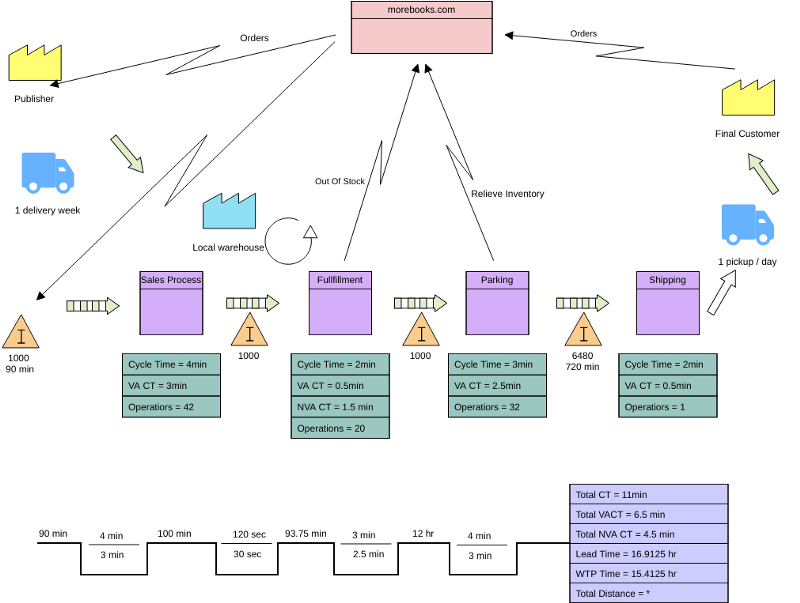
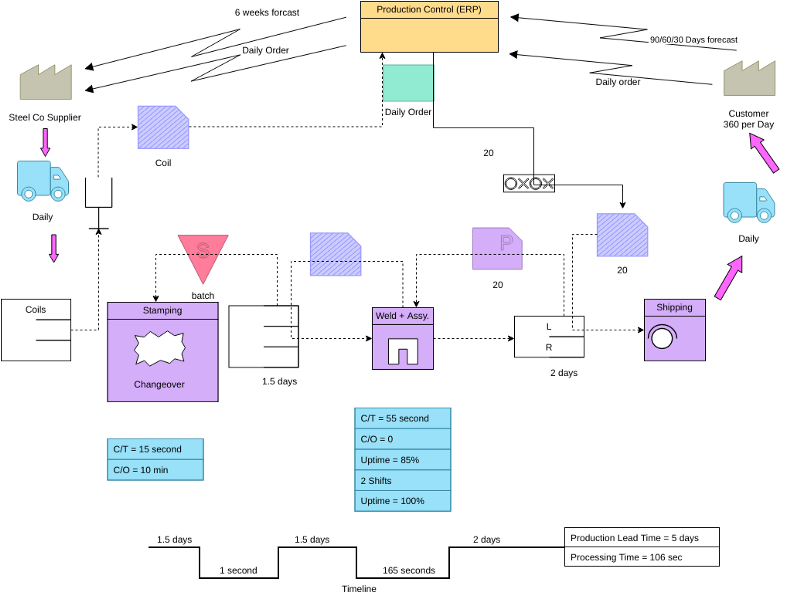
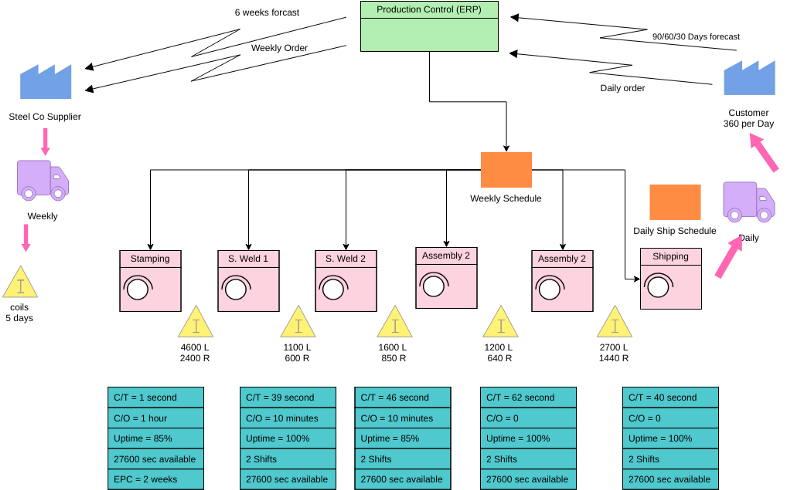
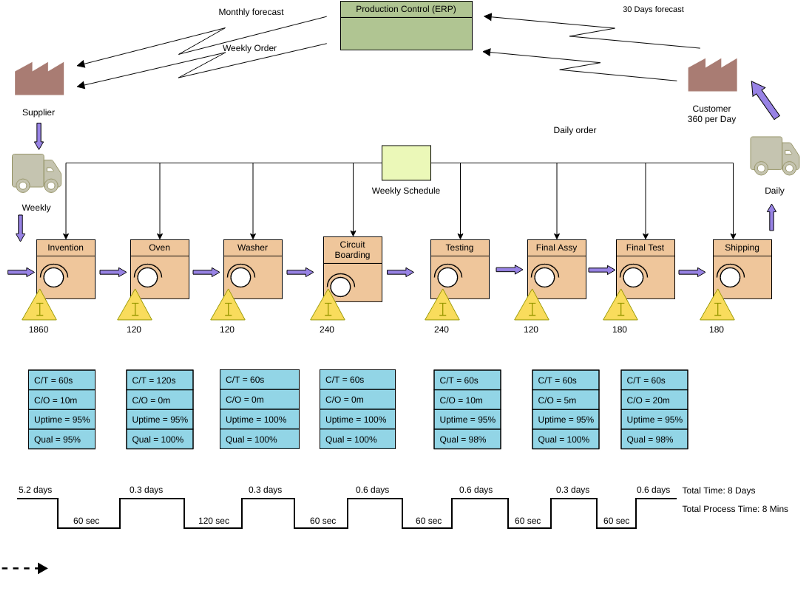
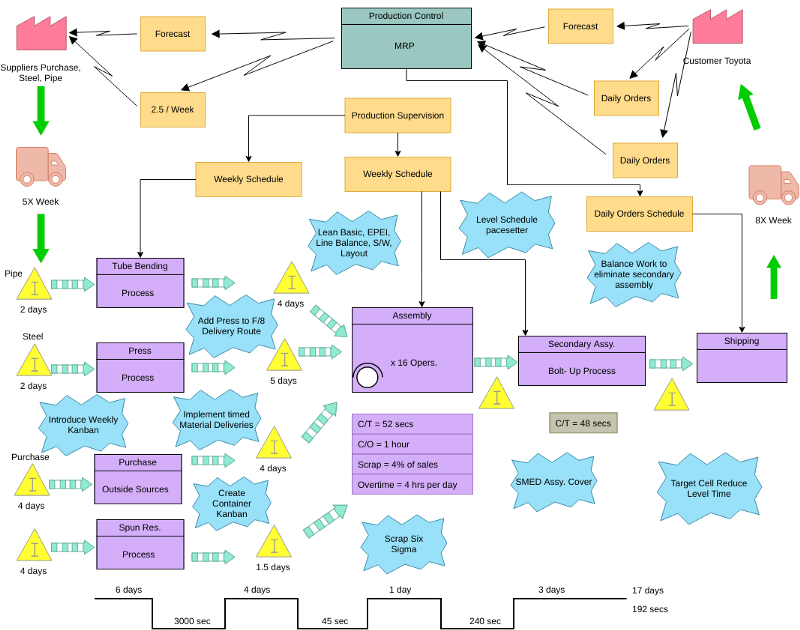
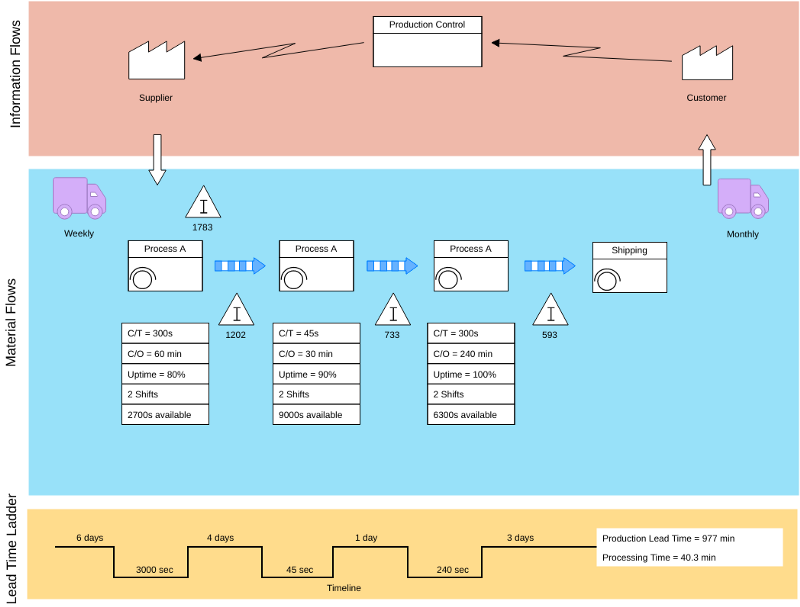
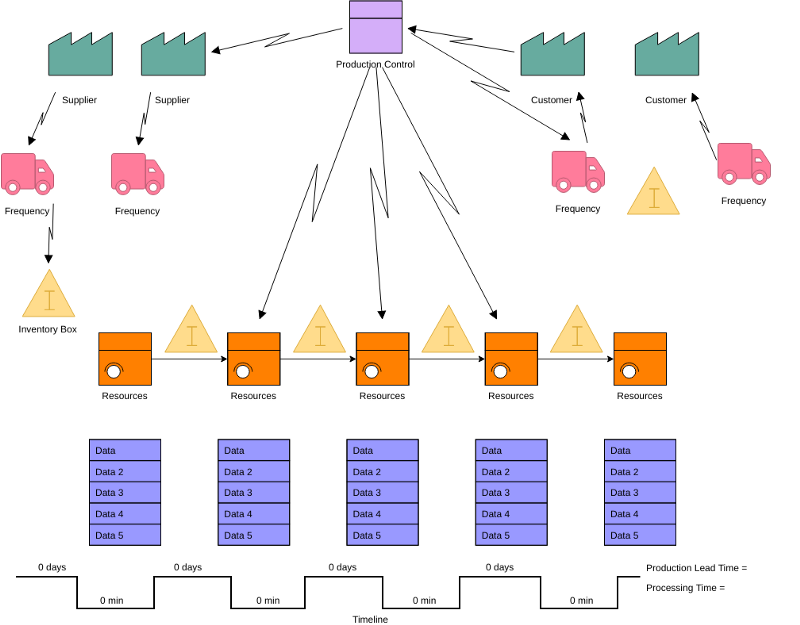
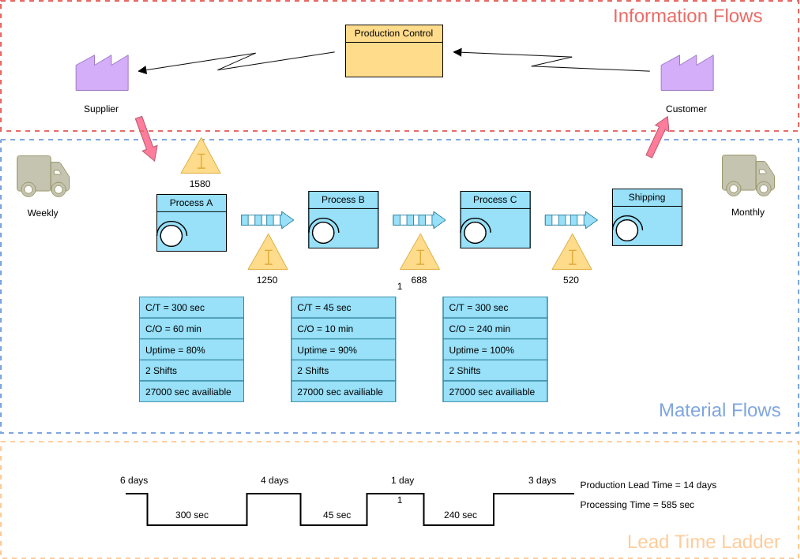
This post is also available in Deutsch, English, Español, فارسی, Français, 日本語, Polski, Portuguese, Ру́сский, Việt Nam, 简体中文 and 繁體中文.