PDCA jest uważane za jeden z najpopularniejszych frameworków do ciągłego doskonalenia procesów biznesowych. PDCA (plan, wykonaj, sprawdź, działaj), znane również jako cykl Deminga, jest najprostszym frameworkiem do poprawy procesów. W zasadzie jest to seria cykli sprzężenia zwrotnego ciągłego doskonalenia – decydujesz, jak to działa, ustalasz, jak to poprawić, w końcu wprowadzasz zmiany i ciągle powtarzasz cykl. Uważam, że PDCA jest najprostszym i najskuteczniejszym sposobem na poprawę twojego przepływu pracy.
Cykl PDCA szeroko stosowany w wielu dziedzinach
Deming uważa, że wysoka jakość nie pochodzi z inspekcji produktów na podstawie wyników, ale z ciągłego doskonalenia opartego na procesie. Później koncepcja ta była stosowana nie tylko w zarządzaniu jakością, ale także szeroko stosowana w zarządzaniu przedsiębiorstwem.
Podejście Toyoty
Cykl PDCA stał się jednym z filarów systemu produkcji just-in-time Toyoty. W ciągu ostatnich dwóch dekad systemy Toyoty stały się jednymi z najbardziej udanych demonstracji szczupłej produkcji z wykorzystaniem PDCA; Aby uzyskać więcej informacji na temat zastosowania PDCA przez Toyotę w metodach Lean, zobacz książkę Jeffreya Lake’a 'Metoda Toyoty’ (2003).
Według Deminga, możesz zastosować PDCA w następujących celach:
- Posiadanie systemu do ciągłego doskonalenia jakości
- Redukcja defektów poprzez wyższy poziom jednolitości jakości
- Zrozumienie, co jakość powinna oznaczać w kontekście
Ciągłe doskonalenie w zarządzaniu jakością
W zarządzaniu jakością cykl PDCA jest również szeroko stosowany i osiągnął dobre wyniki. Dlatego cykl PDCA nazywany jest podstawową metodą zarządzania jakością. Na przykład TQM to proces naukowy, który jest rozwijany i organizowany zgodnie z planem jakości. Proces ten odpowiada cyklowi PDCA i przebiega nieprzerwanie.
PDCA – integralna część Six Sigma
Cykl PDCA to logiczna procedura robocza do efektywnego wykonywania jakiejkolwiek pracy. W zarządzaniu jakością Six Sigma cykl PDCA był szeroko stosowany i osiągnął dobre wyniki, dlatego niektórzy mówią, że cykl PDCA jest podstawową metodą zarządzania jakością. Nazywa się go cyklem PDCA, ponieważ cztery procesy nie są realizowane raz i kończone, ale powtarzane w kółko. Jeden cykl się kończy, niektóre problemy są rozwiązane, inne mogą pozostać nierozwiązane, lub mogą pojawić się nowe problemy, a następny cykl się zaczyna.
Co oznacza cykl Deminga?
Cykl Deminga to czteroczęściowe podejście zarządzające, które promuje ciągłe doskonalenie. Ten i inne podobne modele ciągłego doskonalenia zostały zintegrowane z biznesem i przedsiębiorstwem lub zwinny rozwój.
PDCA to pierwsza litera angielskich słów 'plan’, 'wykonaj’, 'sprawdź’ i 'działaj’. Cykl PDCA to proces zwinnego rozwoju w zarządzaniu jakością w trybie spiralnym, a cykl trwa. Jest to proces iteracyjny i przyrostowy, a nie jednorazowy.
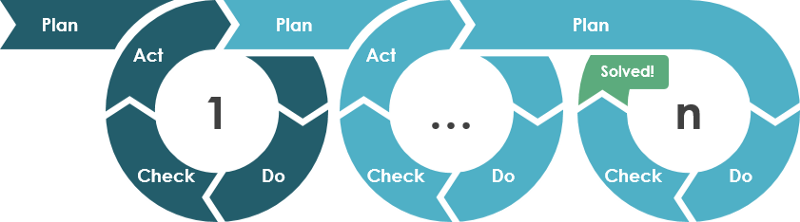
- Plan — Logiczna sekwencja zaczyna się od planu i koncentruje się na częściach strategicznych. Celem jest przedstawienie i analiza informacji w celu ustalenia celów i zadań.
- WYKONAJ — Czas na wdrożenie poprzez realizację tego, co zostało ustalone w poprzednim kroku
- Sprawdź: Po inspekcji sprawdzimy, czy operacja się poprawiła, na przykład, co działa, a co jest nie tak? Czy są jakieś alternatywy lub rozwiązania?
- Działaj: W tym kroku, na podstawie ustaleń z kroku 3, koncepcja PDCA sugeruje ponowne uruchomienie cyklu PDCA w poszukiwaniu ciągłego i nieprzerwanego doskonalenia.
Po zakończeniu kroku 4, musisz wrócić do pierwszego kroku, aby wprowadzić więcej nowych ulepszeń. Jeśli spojrzysz na ewolucyjny cykl kontroli, musisz zrozumieć go jako proces bez końca. Nie ma ani początku, ani końca. Pomocne jest myślenie o Kole Deminga jako o spirali. Spirali, która wznosi się w górę. Każde ulepszenie przenosi twoją firmę na nowy, lepszy poziom.
Znaczenie cyklu PDCA
Każda praca może być traktowana jako cykl PDCA, który:
- Wymaga zaplanowania,
- Wdrożenia planu,
- sprawdzenia wyników, i
- Podsumowania i poszukiwania dalszych ulepszeń.
Każdy wysiłek to czteroczęściowy cykl PDCA, który musi być zaplanowany, wdrożony, oceniony i dalej udoskonalany. Jednocześnie przejdzie do następnego cyklu. Skok jakościowy, nawet mały, może być dokonany tylko w okresie stopniowego doskonalenia. Tylko w ten sposób możemy poprawić naszą każdą pracę i życie.
Jak wdrożyć PDCA
PLAN :
- Analizuj obecną sytuację i zidentyfikuj istniejące problemy;
- Analizuj przyczyny lub czynniki wpływające na problem;
- Zidentyfikuj główną przyczynę problemu lub główny czynnik wpływający;
- Opracuj środki i zaproponuj plany działania;
WYKONAJ :
- Wdroż plan działania;
SPRAWDŹ :
- Ocena wyników (analiza danych);
DZIAŁANIE :
- Standaryzacja i dalsza promocja;
- Ponownie wykorzystaj cykl PDCA w następnej okazji do poprawy;
Ważne jest, abyś nie patrzył na wszystko z indywidualnej perspektywy, ale jako przedsiębiorca zawsze myślał zarówno w małych, jak i dużych cyklach PDCA i działał odpowiednio. Dla ciebie następujące motto musi zawsze być na pierwszym planie.
Podziel cykl PDCA na 8 kroków
- Analizuj status quoaby zidentyfikować istniejące problemy z jakością: magazyn nie jest standardowy, jest zatłoczony i bałaganiarski.
- Analizuj różne przyczynylub czynniki wpływające, które powodują problemy z jakością: 1. Jest więcej materiałów i mniej półek. 2. Obszar nie jest jasny.
- Zidentyfikuj główne czynniki wpływające na jakość: 1. Dodaj półki. 2. Ponowny podział obszarów.
- Skierowane nagłówne czynniki problemów z jakością: 1. Opracuj środki i zaproponuj plany działania. 2. Opracuj podział obszaru.
- Wdrażaj plan działania: 1. Dodaj półki, 1. zorganizuj materiały. 2. Podziel obszar i posortuj materiały zgodnie z podziałem obszaru.
- Wynik oceny(dane analityczne): Sprawdź podział obszaru i sporządź podsumowanie.
- Standaryzacja i dalsza retrospektywna analiza: komunikuj wyniki z pracownikami działu i sporządzaj zapisy.
- Podnieś nierozwiązane problemy w tym cyklu, i przekaż je do następnego cyklu PDCA: jeśli plan nie może być zrealizowany, przekaż go do następnego cyklu poprawy.
Hierarchiczna struktura cyklu PDCA dla dużej organizacji
- Duży pierścień ma w sobie mały pierścień. Jeśli cała firma działa jako jeden duży cykl PDCA, to każdy z jej działów, grup i ich własnych małych cykli PDCA jest w niego wbudowany, tworząc hierarchię PDCA.
- Ciągłe doskonalenie cyklu PDCA – cykl PDCA nie jest na tym samym poziomie cyklu, każdy cykl rozwiązuje część problemu, osiąga część wyników, pracuje nad dalszym, poziomem jednego kroku. W następnym cyklu są nowe cele i treści, aby drabina mogła nadal rosnąć.
Podsumowanie
Cykl PDCA to naukowa procedura i integralna część zarządzania jakością całkowitą, metody lean, six sigma i innych metod. Na przykład cały proces działań zarządzania jakością całkowitą to proces formułowania i organizacji planu jakości. Proces ten jest realizowany zgodnie z cyklem PDCA, jest ciągłą, powtarzalną operacją. Cykl PDCA nie jest stosowany tylko w systemie zarządzania jakością, ale także w każdym postępowym zarządzaniu.
Najlepsze darmowe narzędzie do projektowania wizualnego w jednym
Nawet jeśli nie jesteś profesjonalnym projektantem, możesz łatwo tworzyć wpływowe infografiki, ulotki, plakaty, CV i broszury. Zrób to sam, twórz jak profesjonalista, korzystając z kompleksowego rozwiązania do projektowania wizualnego InfoART. Teraz możesz tworzyć profesjonalne infografiki, ulotki i materiały marketingowe w kilka minut, bez doświadczenia w projektowaniu!
Wykonaj pracę przy minimalnym czasie i wysiłku
Twórz profesjonalne treści szybciej i lepiej:
- Funkcje: Komponent układu i edytor typu przeciągnij i upuść umożliwiają szybkie tworzenie i ponowne edytowanie dowolnego projektu.
- Zasoby w narzędziu: Oszczędzaj czas na znajdowaniu zdjęć lub clipartów, ponieważ wszystko, czego potrzebujesz, jest już zawarte w InfoART. Po prostu wykonaj wyszukiwanie, aby to uzyskać.
- Szablony: Nie musisz tracić czasu na projektowanie, ponieważ dostępny jest bogaty zestaw profesjonalnie zaprojektowanych szablonów.
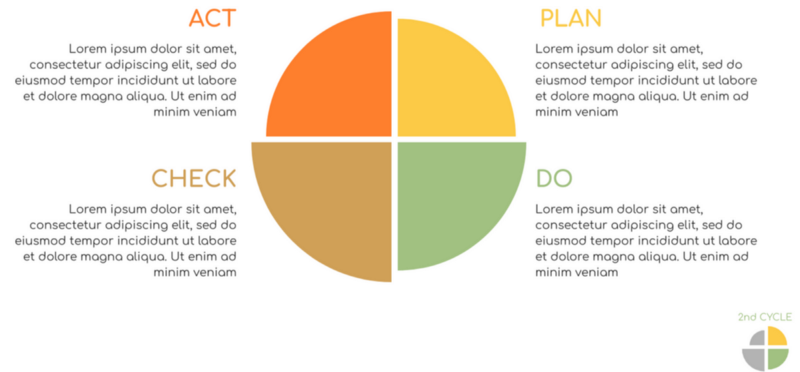
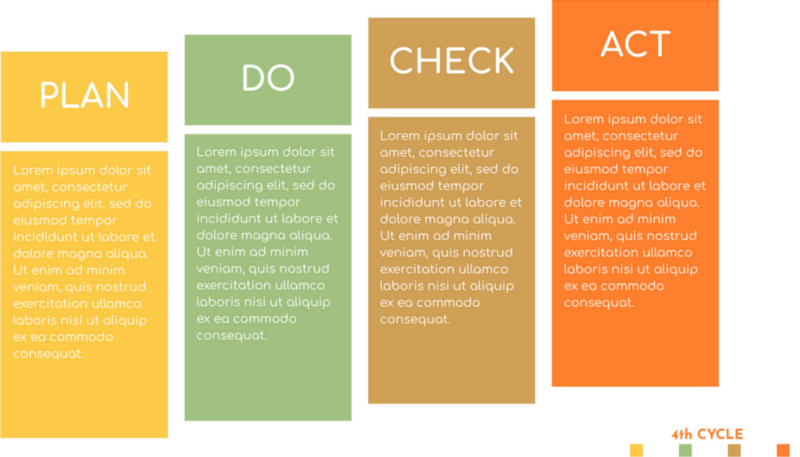
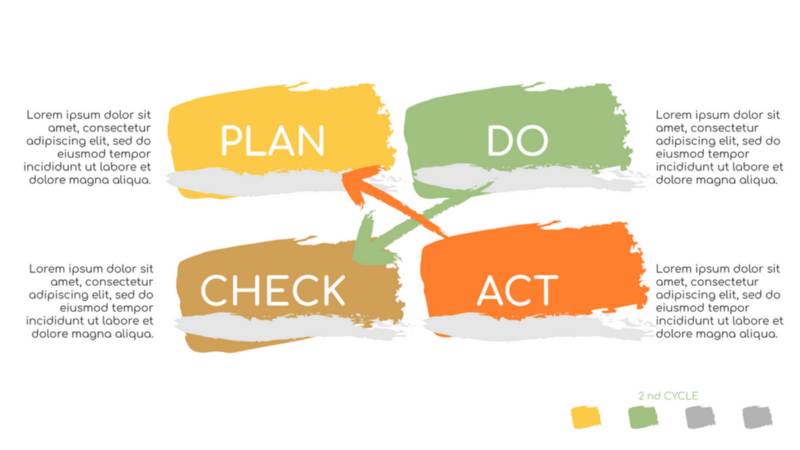
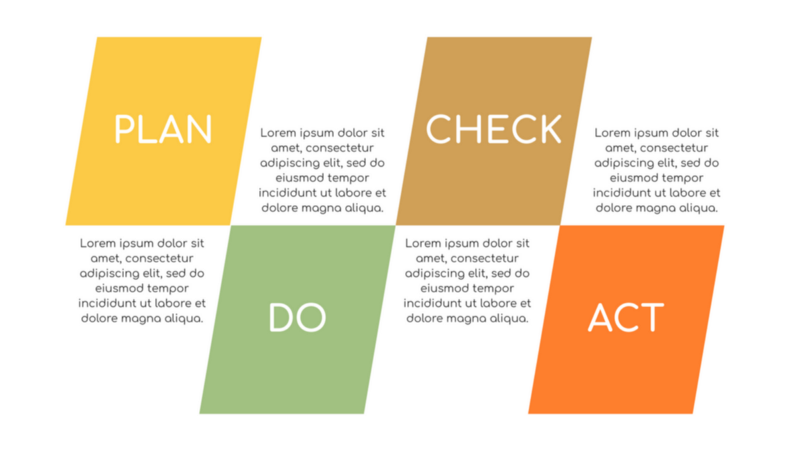
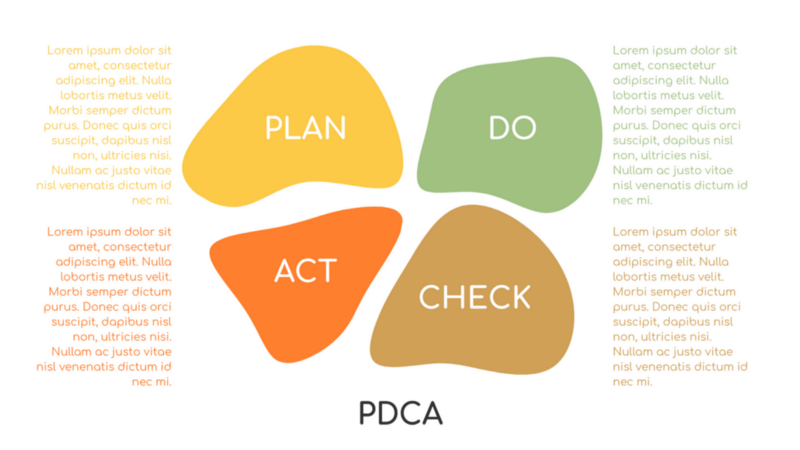
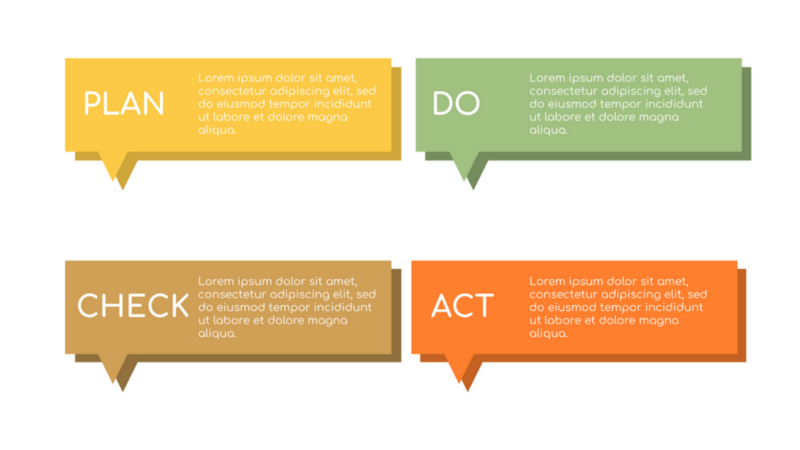
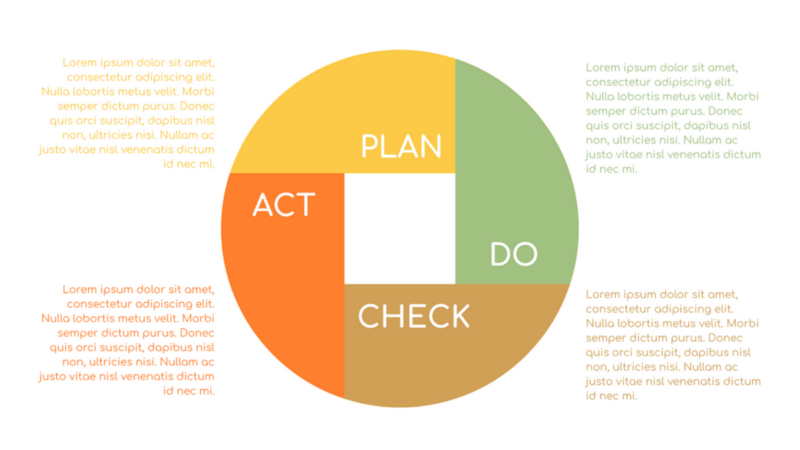
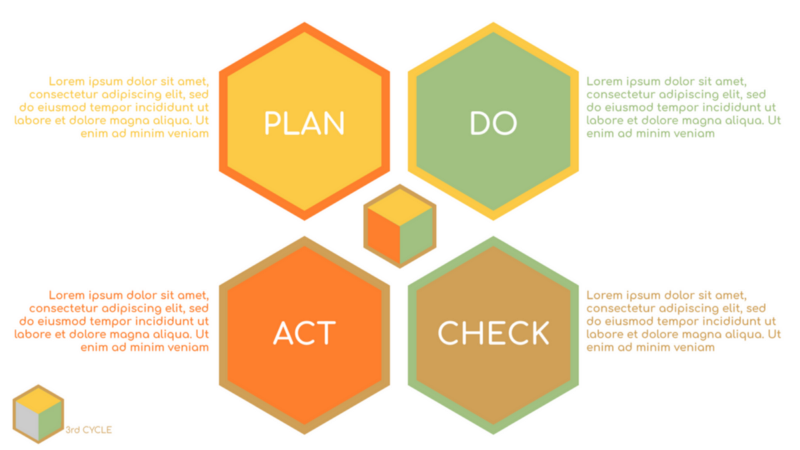
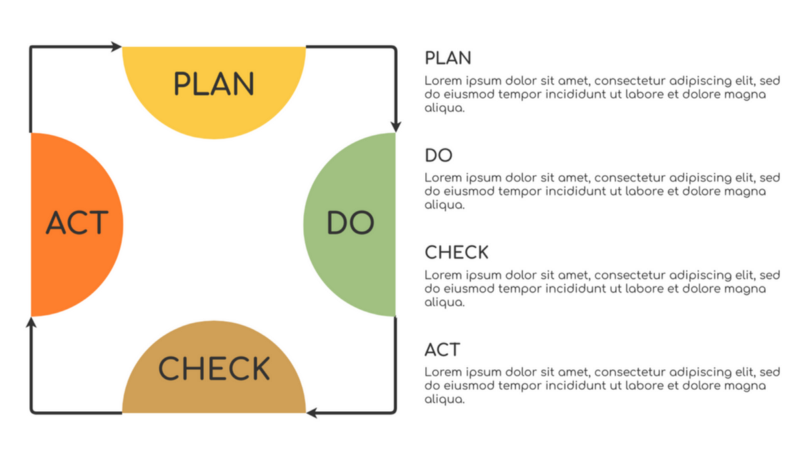
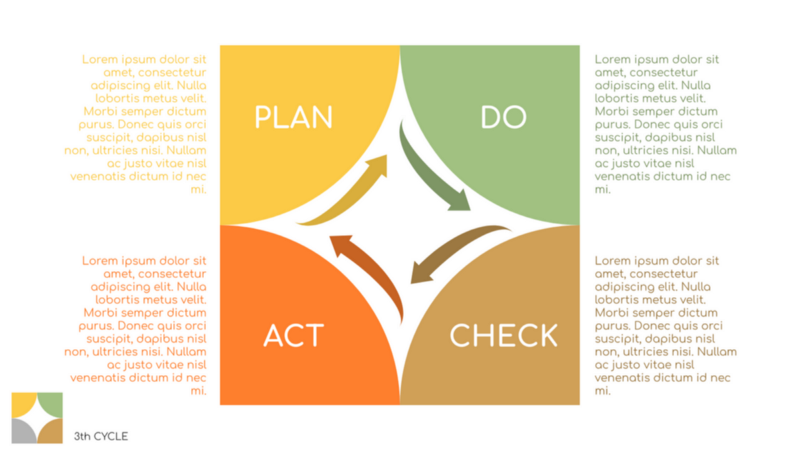
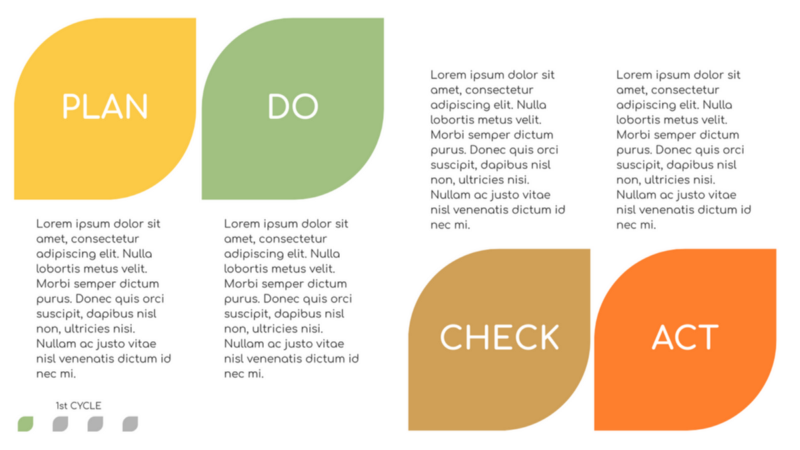
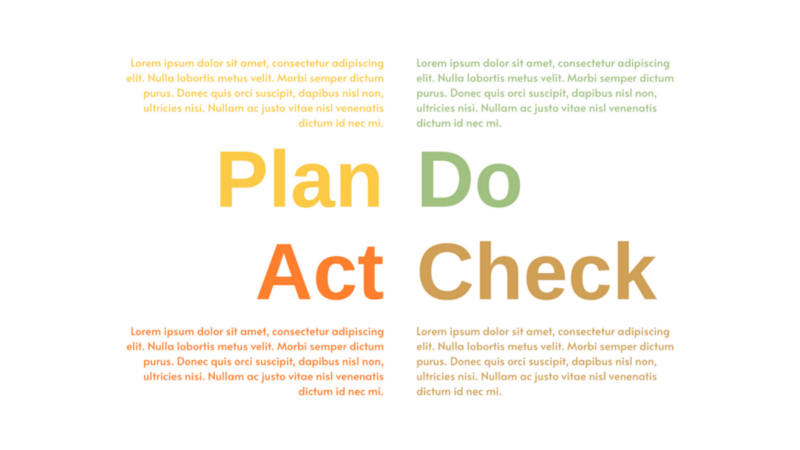
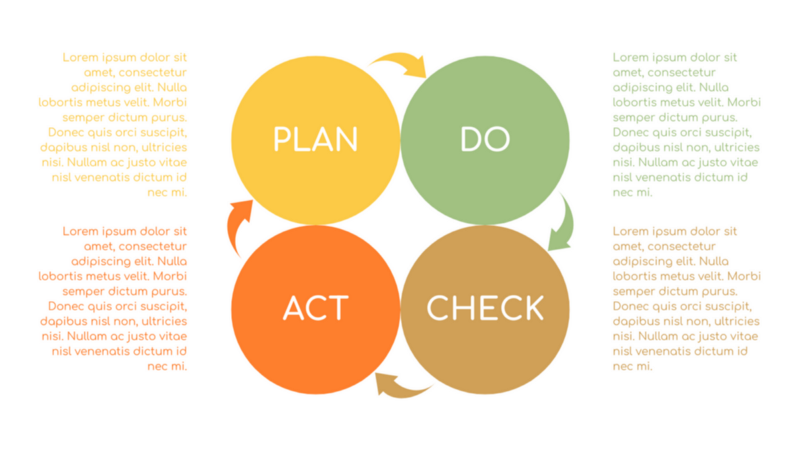
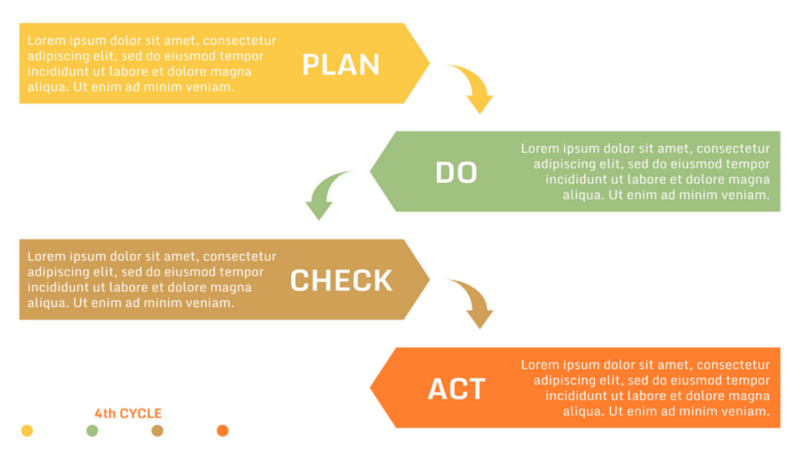
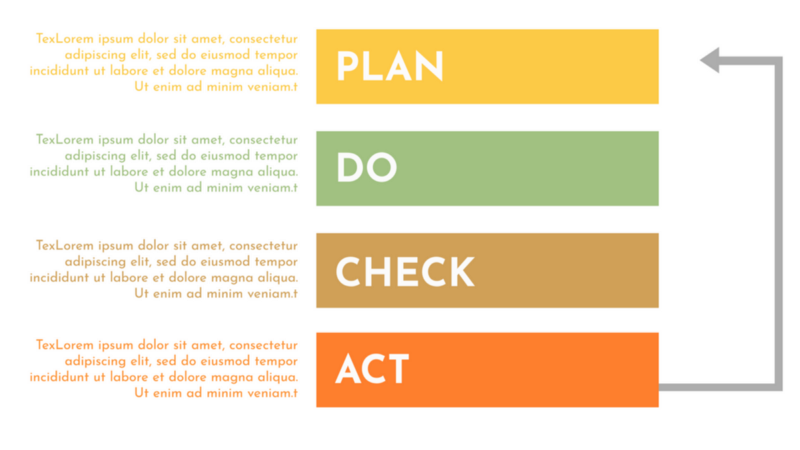
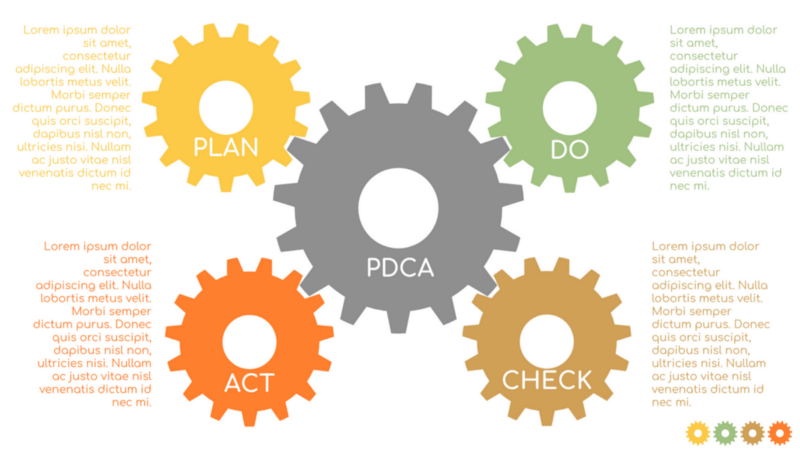
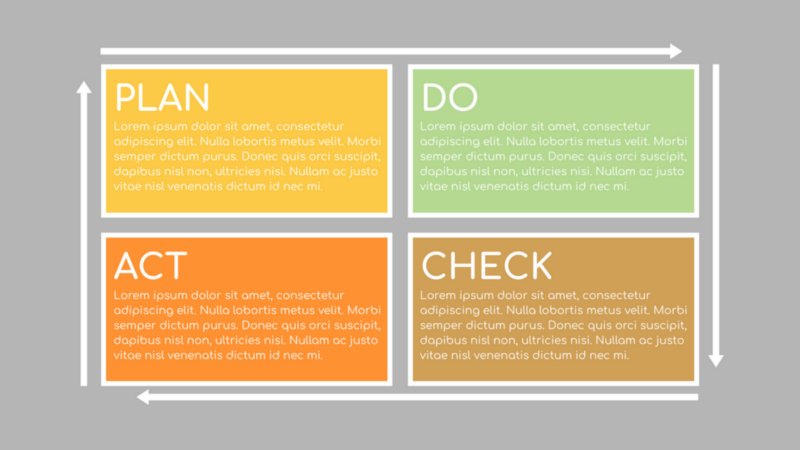
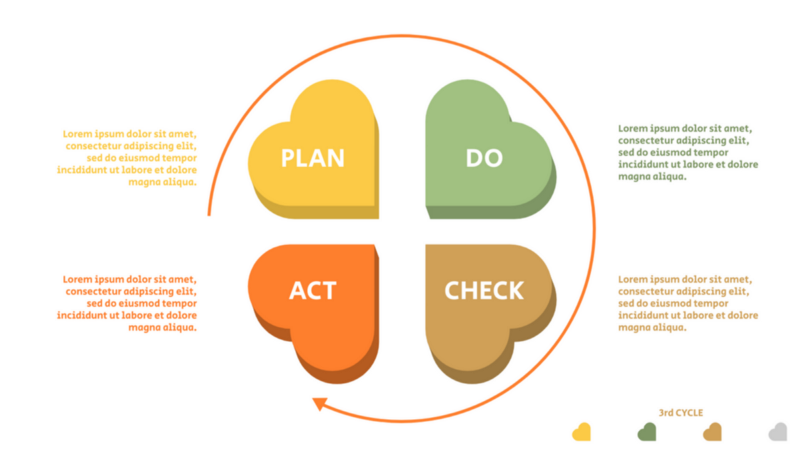
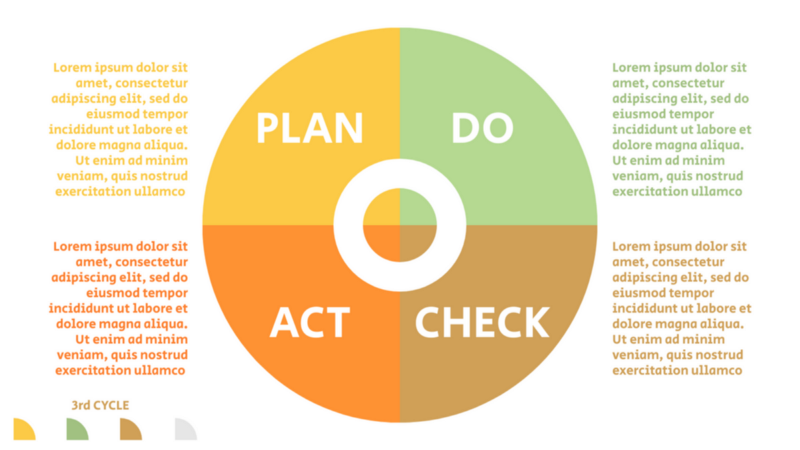
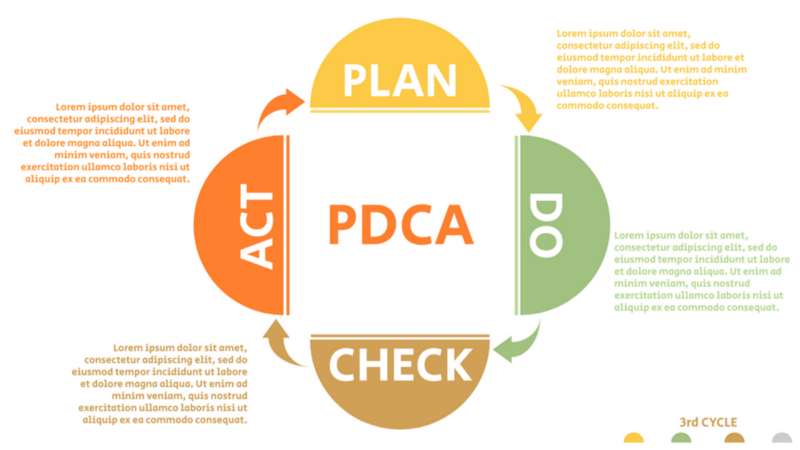
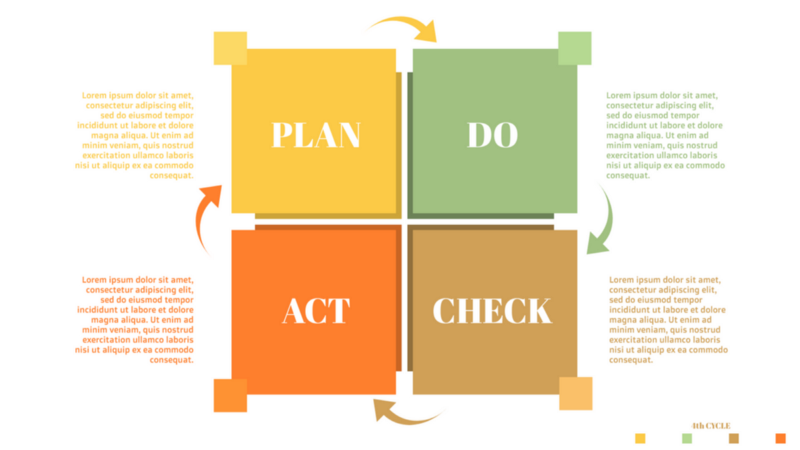
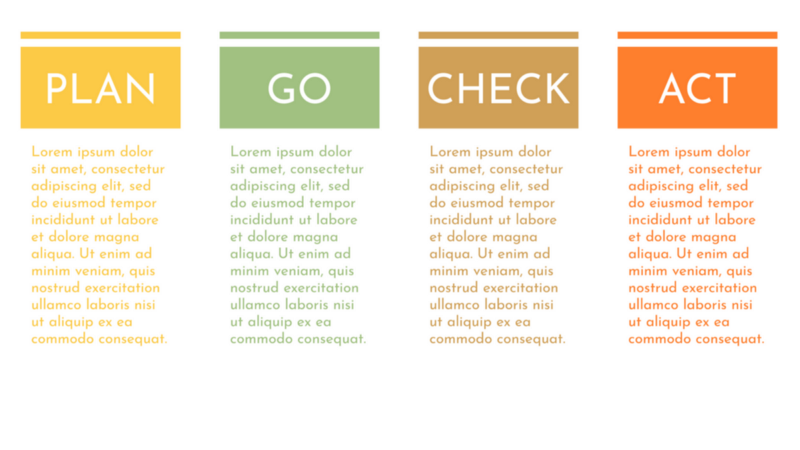
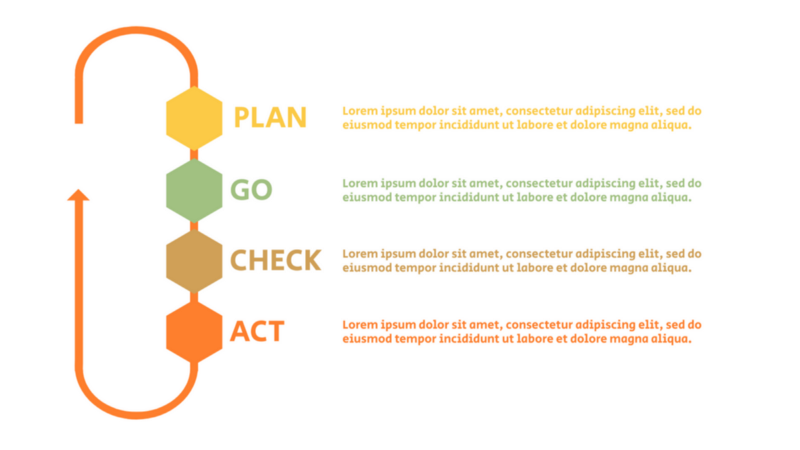
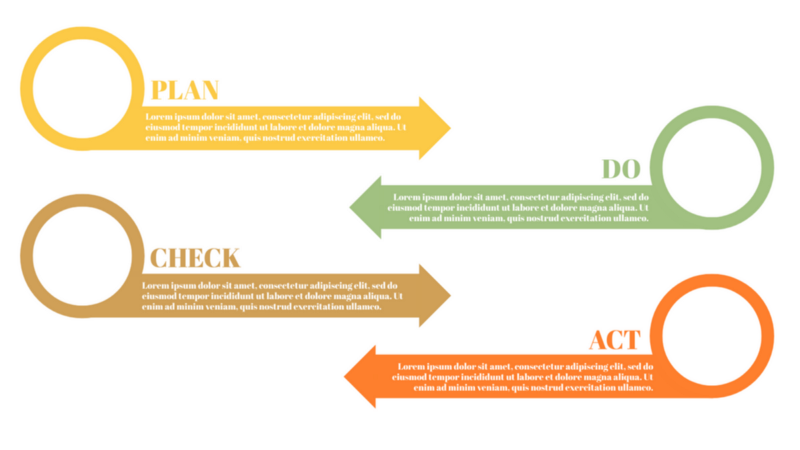
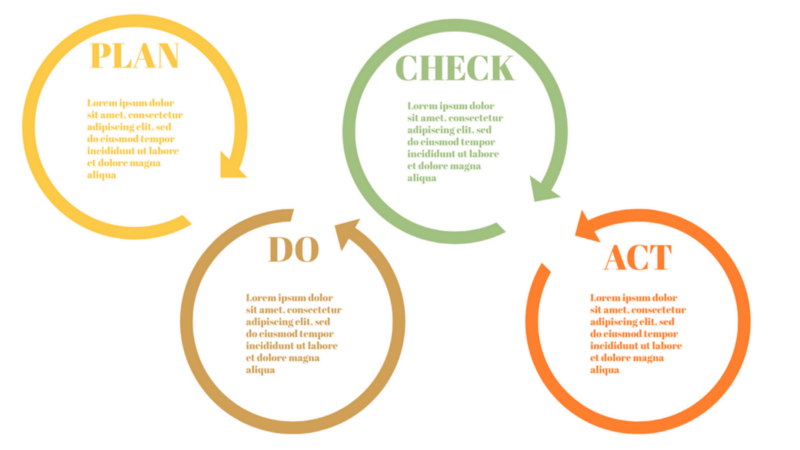
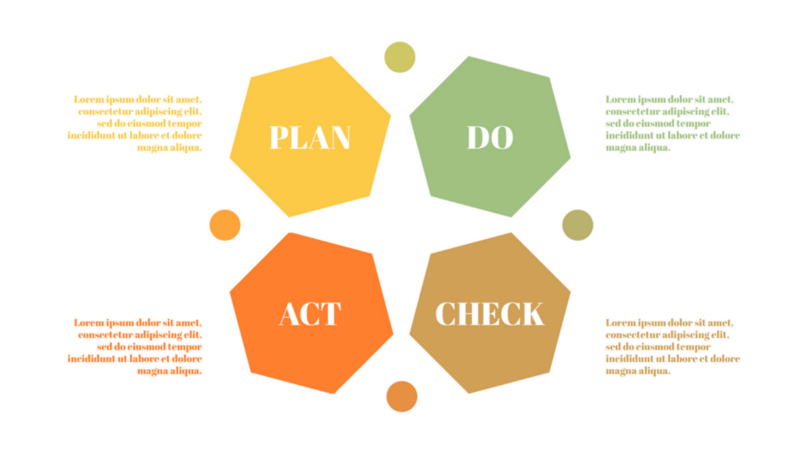
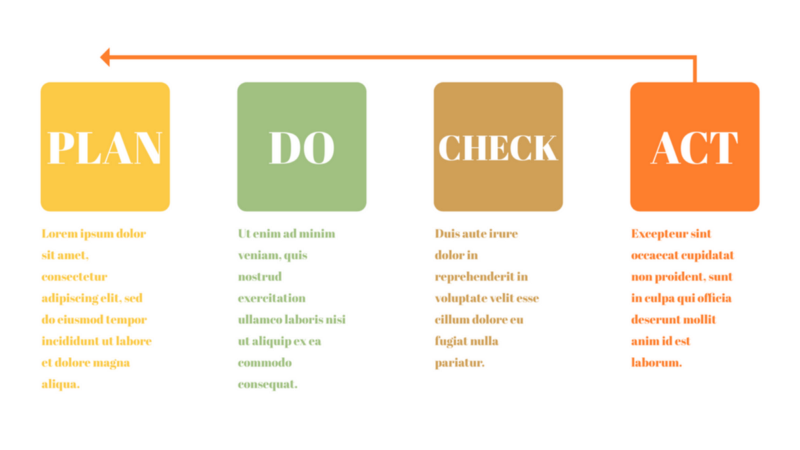
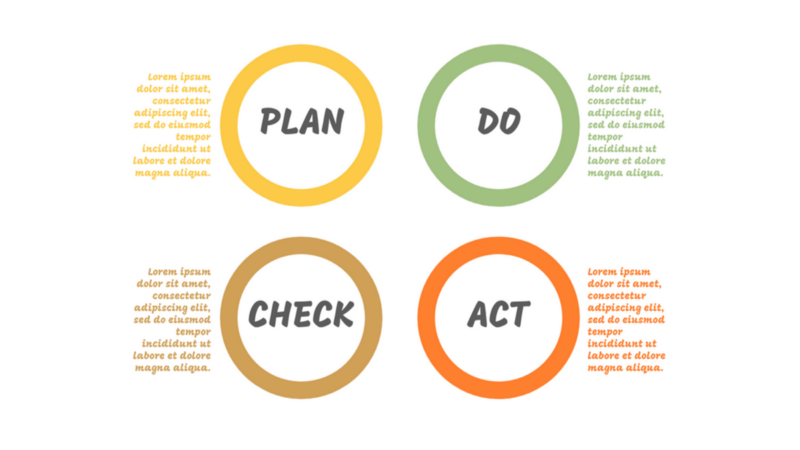
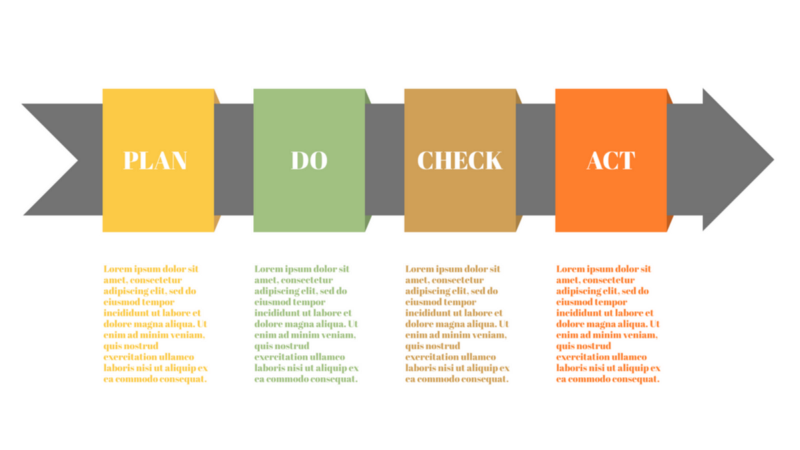
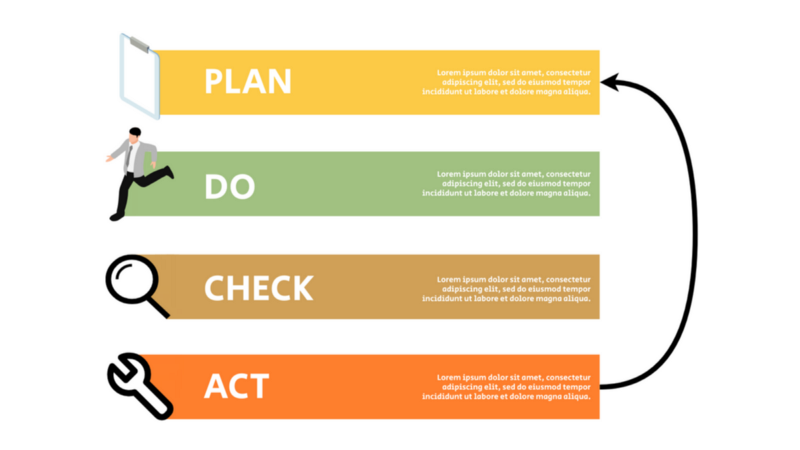
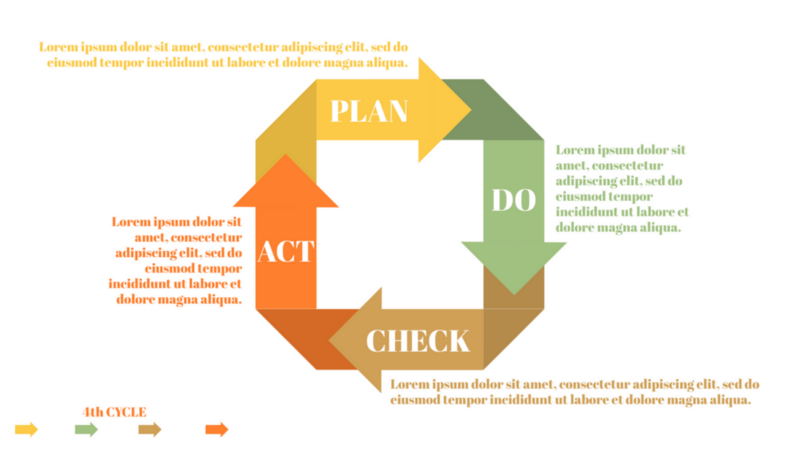
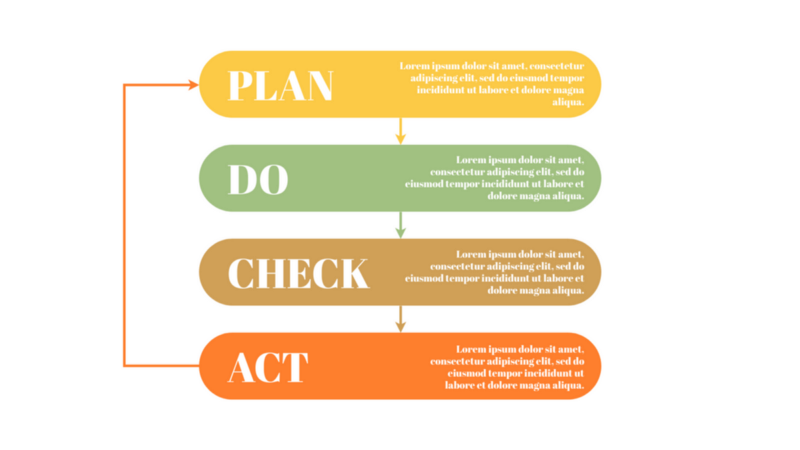
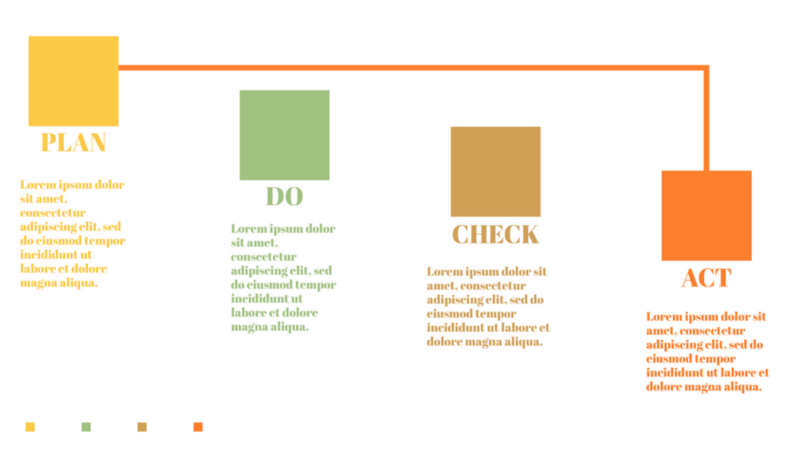
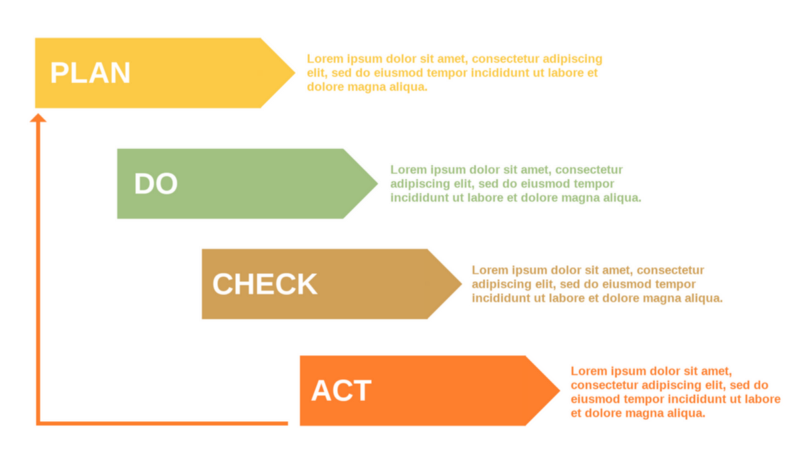
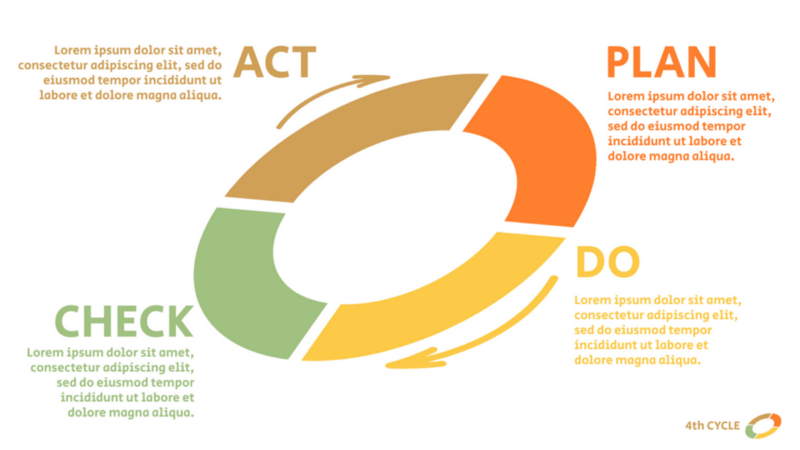
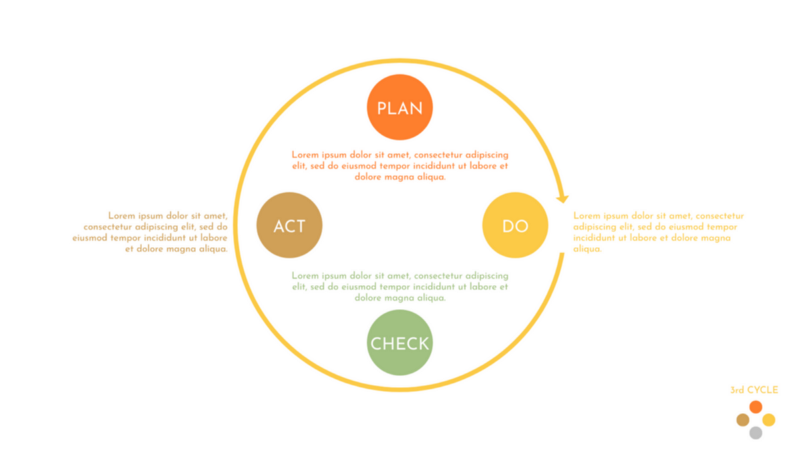
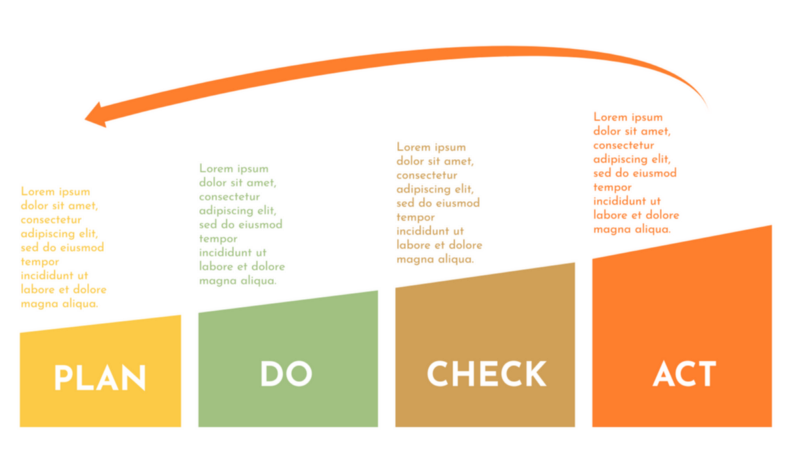
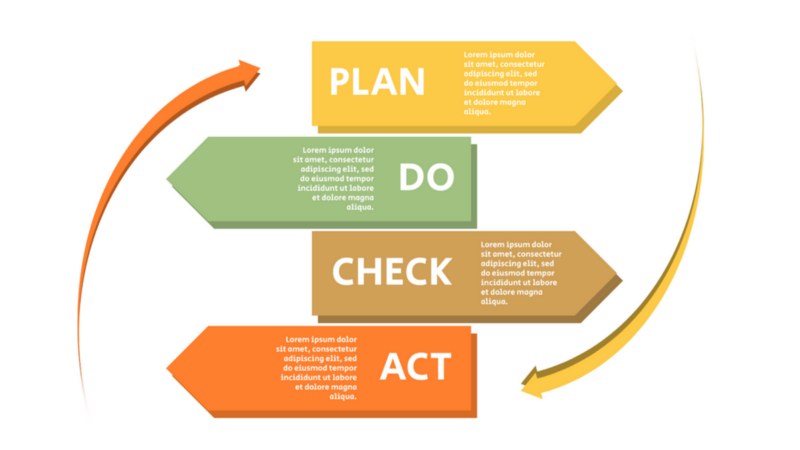
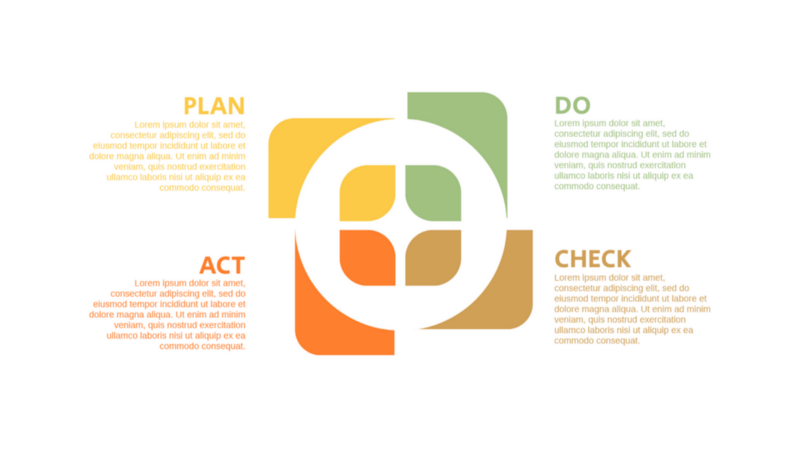
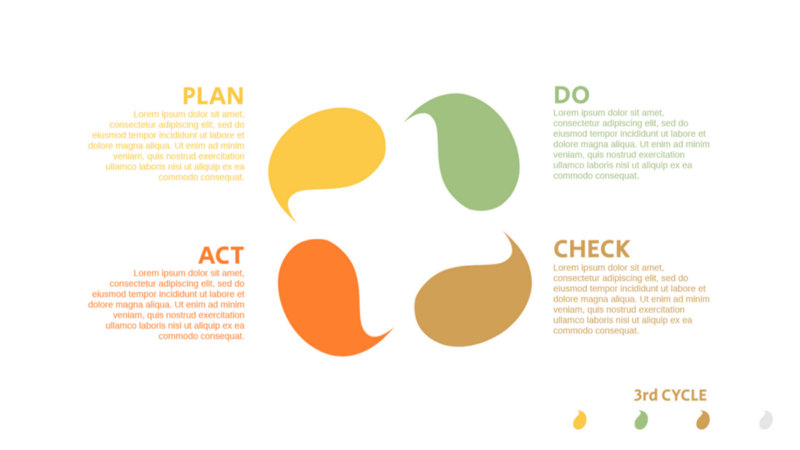
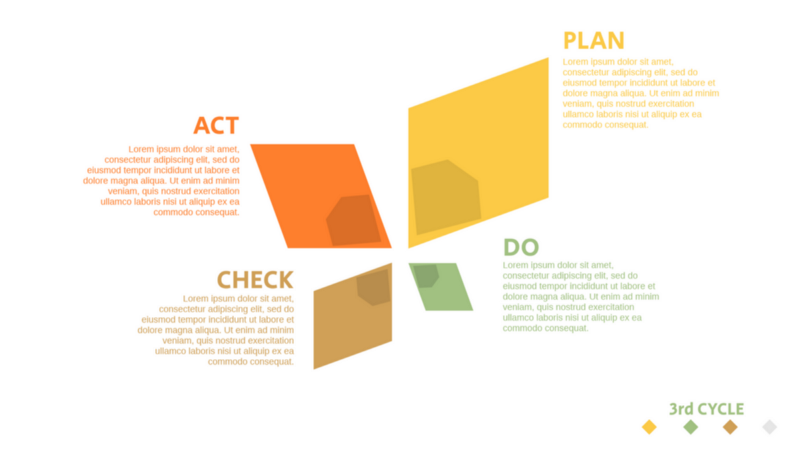
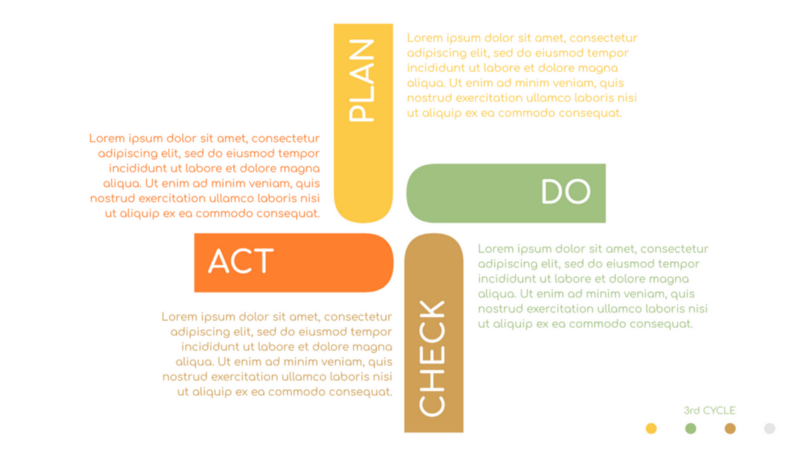
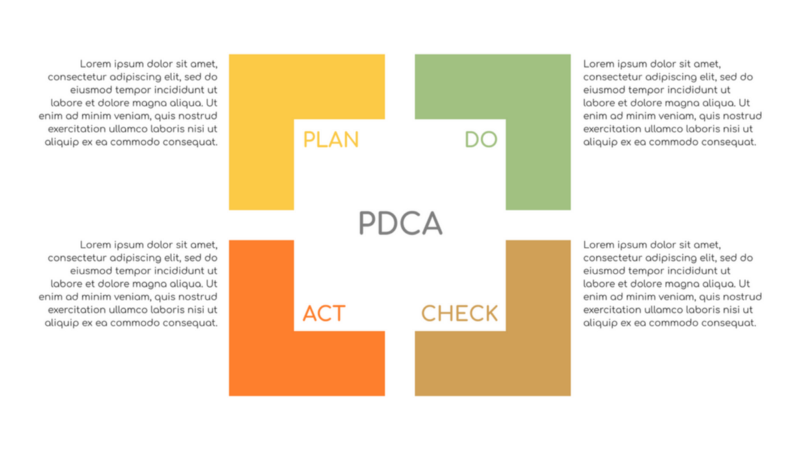
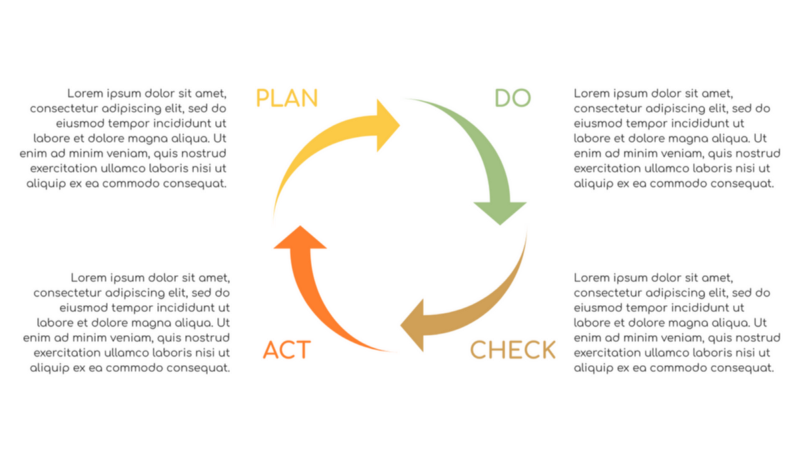
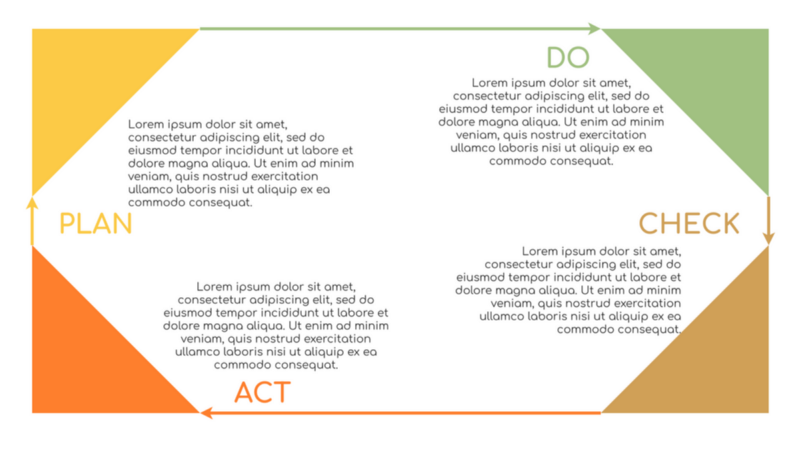
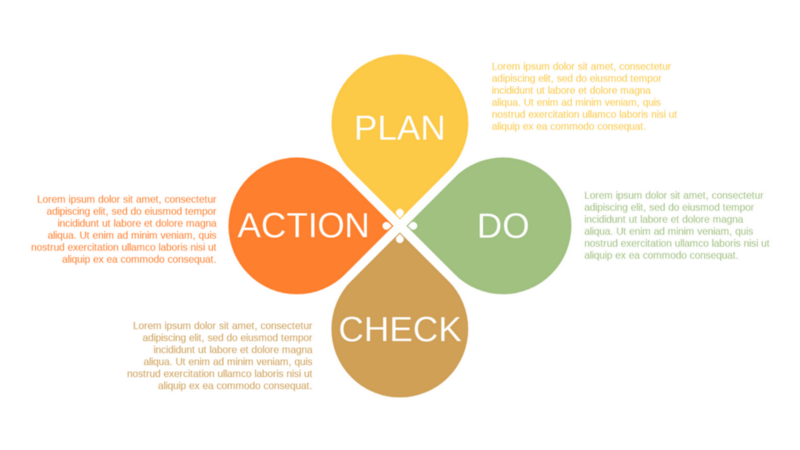
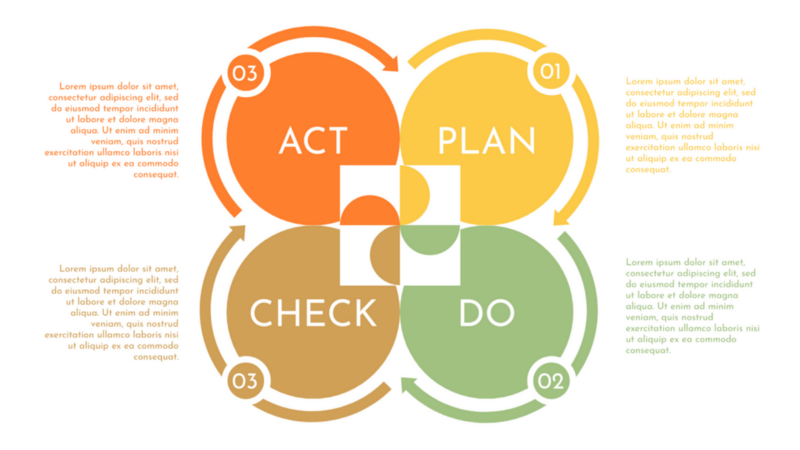
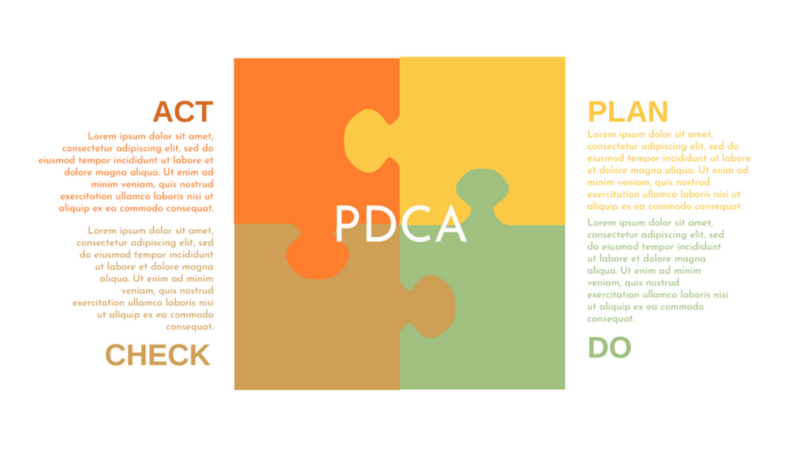
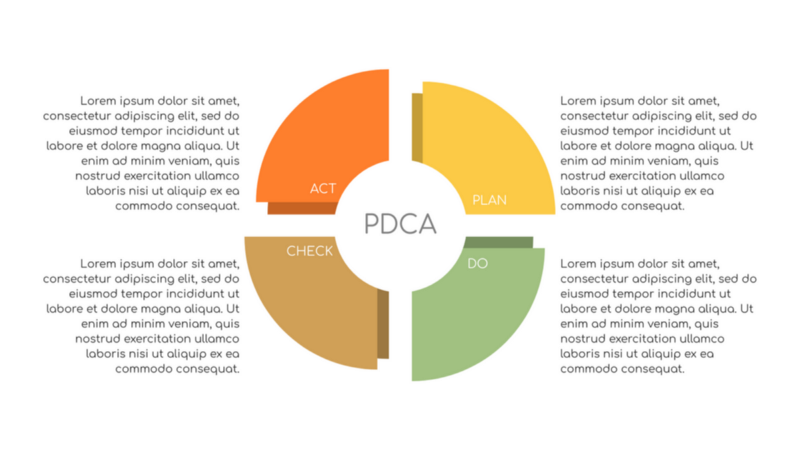
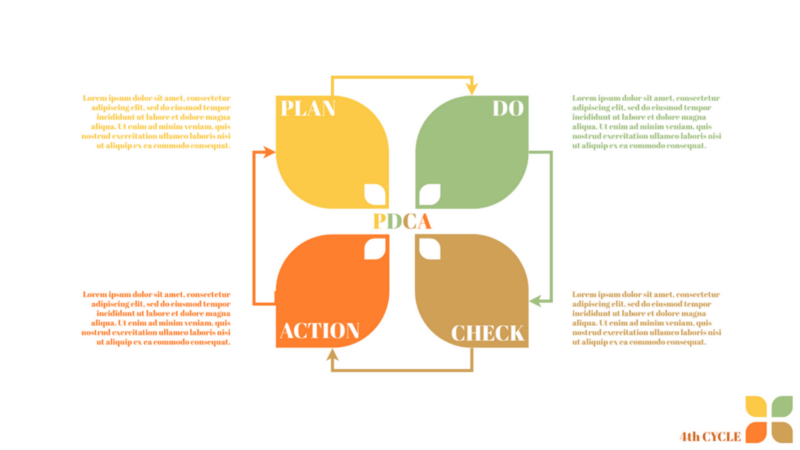
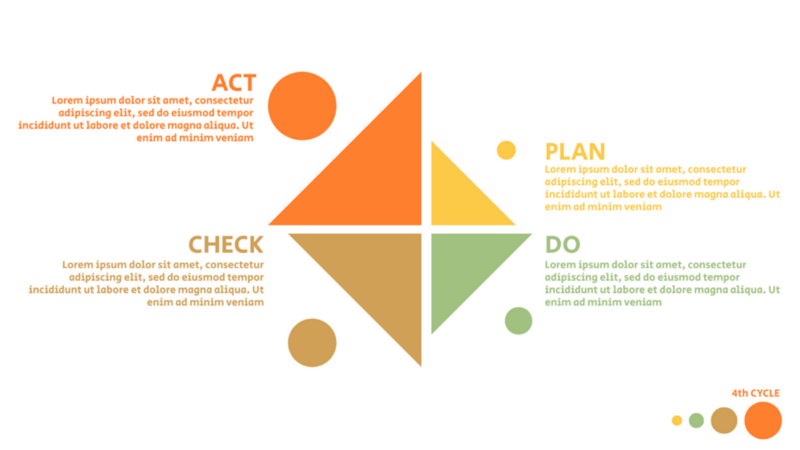
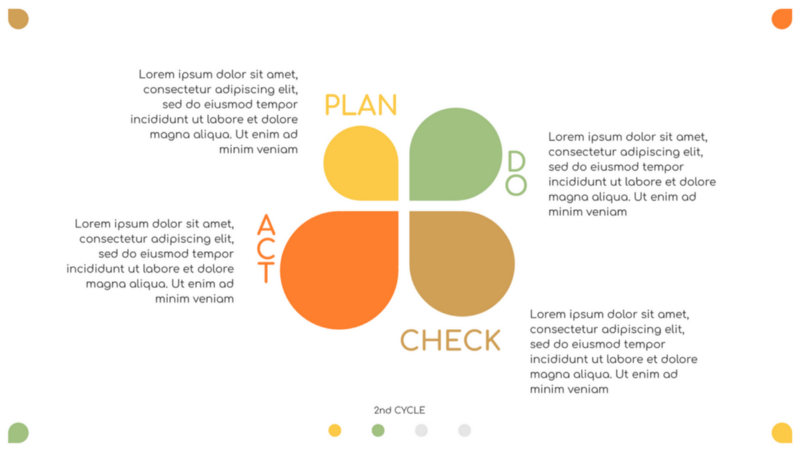
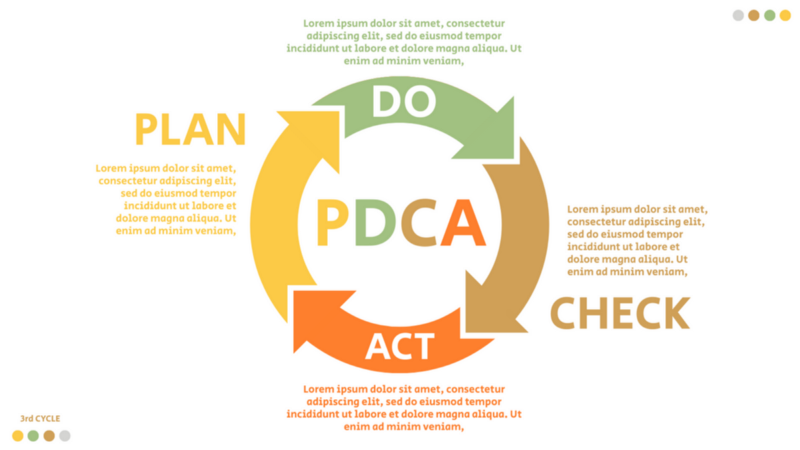
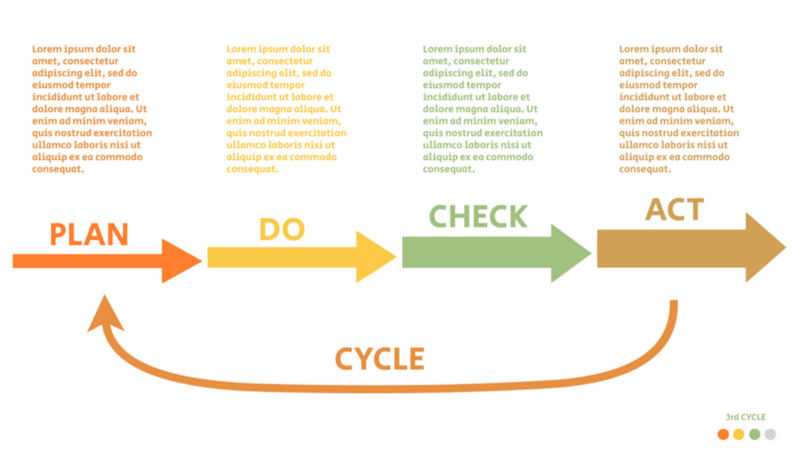
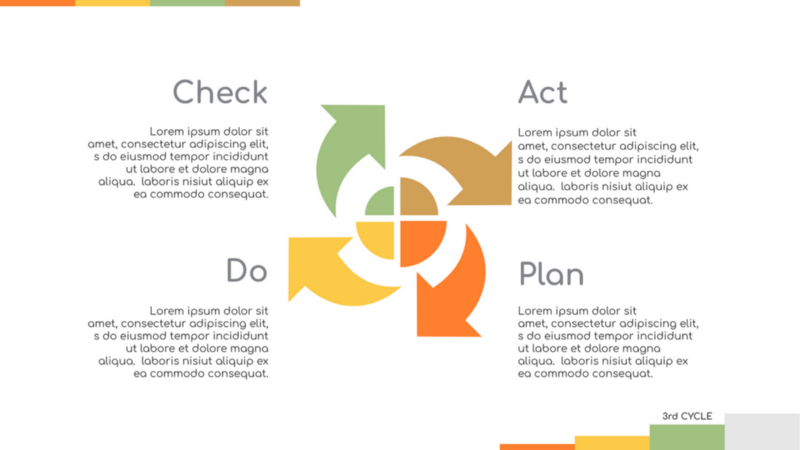
Ten post dostępny jest również w Deutsch, English, Español, فارسی, Français, Bahasa Indonesia, 日本語, Portuguese, Ру́сский, Việt Nam, 简体中文 and 繁體中文